In 1986, the company Motorola was so troubled by manufacturing defects that its engineer, Bill Smith, came up with a whole methodology to reduce the number of defects to a statistical error. This is how the Six Sigma method emerged, which soon became adopted by other industrial and financial giants.
Six Sigma is a concept from probability theory expressed by the formula: no more than 3.4 defects per million products or processes. The mathematical task of the methodology is to reduce variability.
In the literal sense, Six Sigma is a project management methodology focused on eliminating production defects as a category.
The Statistical Goal of Six Sigma
Principles
- Make processes predictable.
- Strive to ensure that manufacturing and business processes can be described, measured, analyzed, improved, and controlled.
- To achieve success with Six Sigma, involve the entire organization, especially top management.
- Set specific, measurable goals: reduce costs by 20%, increase profitability by a third, or decrease the production cycle by an hour.
- Involve managers with strong leadership qualities and the ability to listen to partners.
- Make decisions based on verified information and statistics rather than assumptions.
Algorithms
Six Sigma offers two approaches depending on whether you are improving a process (DMAIC) or creating a new product (DMADV, also known as DFSS). Both methods can be described by the formula “Plan-Do-Check-Act.”DMAIC Algorithm
- Define the project goals and customer needs. Form a project team, establish its area of responsibility, and allocate authority.
- Collect current data and “measure” the key parameters of the process.
- Analyze the collected information and identify the factors that affect the organization’s quality or business activity. Find the root cause of defects and suggest ways to eliminate them.
- Improve or optimize current processes. Make trial changes.
- Control your adjustments so that any deviations from the goal do not lead to defects again. Report the project’s progress on information boards and monitor how the team works with statistics. Repeat the process until you achieve the desired quality.
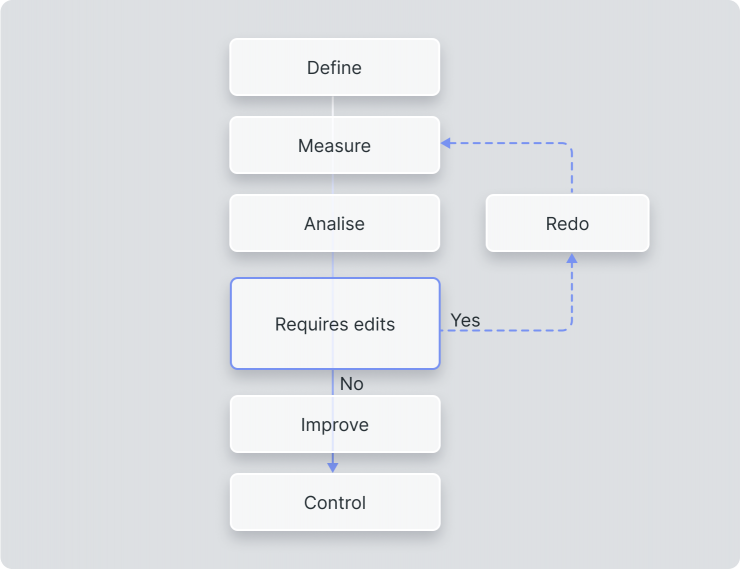
DMAIC Algorithm
DMADV or DFSS Algorithm
1 Define the goals that should align with customer desires and the enterprise strategy. Create a project team.
2 Outline the product’s key characteristics and the requirements for the production cycle.
3 Find and analyze several options.
4 Choose the best option and start working on it.
5 Implement the project in practice.
2 Outline the product’s key characteristics and the requirements for the production cycle.
3 Find and analyze several options.
4 Choose the best option and start working on it.
5 Implement the project in practice.
Tools
You can use both quality management principles and statistical methods. Key management principles include:- “5 Whys”: Keep asking “why” until you identify the root cause of defects.
- Business Process Map: Create a schematic representation of the resources available and what needs to be done. For example, here’s a process map for ordering and sending a product.
- Cost-Benefit Analysis: When multiple project options are available, select the one with the best benefit-to-cost ratio.
- Critical-to-Quality (CTQ) Tree: Draw a schematic with the key characteristics for your project.
Statistical tools include:
1Analysis of variance2 Regression analysis
3 Scatter diagram
4 Control chart
5 Pareto chart
Hierarchy
The Six Sigma management concept resembles Eastern martial arts. The role of the executor depends on their belt – their level of Six Sigma knowledge and skills.
- Top Management: Allocates responsibilities and resources. It removes internal corporate barriers and combats the personnel’s natural resistance to change.
- Champions: Implement the methodology within the organization and mentor Black Belts.
- Master Black Belts: Oversee the implementation of Six Sigma and command regular Black Belts.
- Black Belts: Work on the project and fulfill assigned tasks under the Master’s guidance.
- Green Belts: Employees who, besides their main duties, work on implementing the methodology under the supervision of Black Belts.
- White and Yellow Belts: Employees who have basic knowledge of Six Sigma and either partially participate in the project or observe the actions of experienced colleagues.
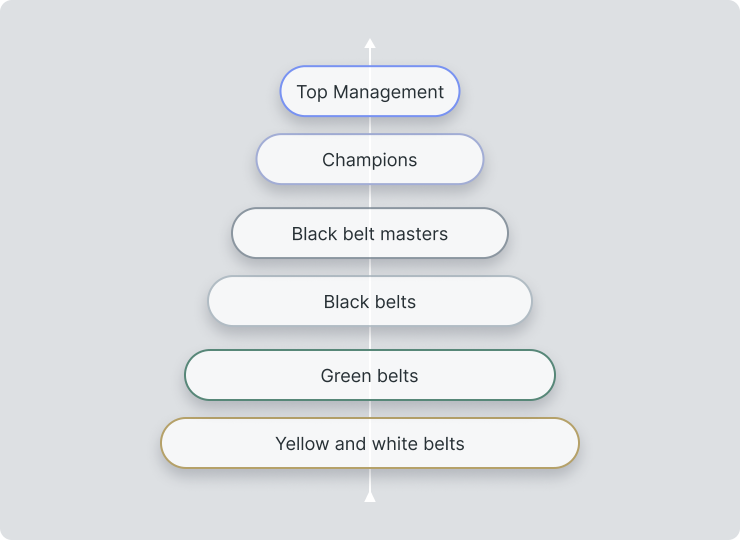
Certification can be obtained through companies like ASQ and IISE. Training takes place both on-site in the USA and online. Exams can also be taken from your computer using specialized software.
Differences from Similar Methodologies
Since the late 2000s, the Lean Six Sigma methodology, combining Lean production approaches and Six Sigma, has become popular. Lean aims to reduce costs and eliminate work processes that do not add value to the consumer. It also helps standardize production.
The Six Sigma methodology focuses on reducing defects and requires strict process control. Six Sigma, with its statistical analysis, is practically a technical discipline compared to Lean, which uses more visual control and changes the organization of the workplace.
Six Sigma and Lean are often compared with another methodology (for many, this is more of a corporate philosophy) – Kaizen. It also requires continuous improvement and process standardization. However, the main difference in Kaizen is the emphasis on quick and simple solutions, discussed openly with the staff.
Drawbacks
1 More organizations began training future Black Belts. As a result, critics believe the quality of certification has decreased, and Black Belts are released with fewer skills.
2 Fortune magazine claimed that almost all of the 58 large companies that declared allegiance to Six Sigma later fell out of the S&P 500 index. The methodology, according to the publication, does not help create breakthrough products and technologies.
3 It might limit creative freedom. Constant “measurements” and statistical analysis prevent the project team from brainstorming and coming up with unexpected ideas. The methodology follows a strict algorithm and pursues commercial rather than innovative goals.
4 Six Sigma’s focus on statistics is also a subject of criticism. Theoretical debates revolve around some tools that may not fully consider risks.
What is Six Sigma in Time Management?
Six Sigma identifies two types of time – lead time and cycle time.
- Lead Time: The time elapsed from the moment the client requests a product/service until they receive it.
- Cycle Time: The number of hours required for the entire production cycle or process work.
Implementation by Large Companies
Motorola developed the Six Sigma methodology to reduce costs related to defects. It saved $16 billion from 1986 to 2001 using Six Sigma.Ford increased its revenue by $300 million in 2000 through Six Sigma, creating successful projects that satisfied its customers.
General Electric trained its managers for 100 hours in Six Sigma. By 1997, the corporate profit grew by $700 million. Over three years, GE gained an additional $4.4 billion.
Bank of America used Six Sigma principles in 2005 to improve lead times for opening online accounts, increasing their profit by 30%.
Books
- “Solving Complex Industrial Problems Without Statistics” by Ralph Polak (2016): For those not strong in the statistical part of Six Sigma, offering 14 practical examples of “qualitative thinking.”
- “The Six Sigma Way” by Pande, Neuman, and Cavanagh (2005): A practical guide from three trainers who worked at GE.
- “Lean Six Sigma” by Michael L. George (2007): Describes how to use Six Sigma and Lean to improve quality and reduce production time.
- “Six Sigma for Dummies” by Craig Gygi (2008): A beginner-friendly introduction to the methodology.
Applications and Software
Worksection: A SaaS project management service that allows managing projects, tasks, and checklists. Implement Six Sigma tools by creating improvement plans using checklists or subtasks, assigning responsibility for modernization, and monitoring progress in real time.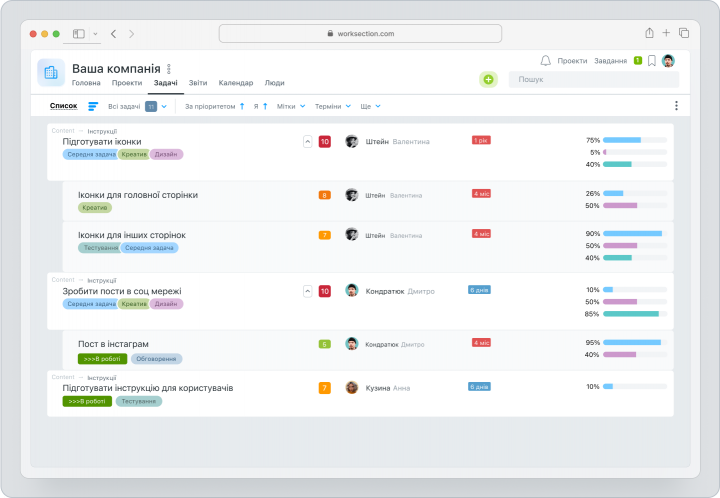