Kaizen (改善) – The Japanese Management Method
Kaizen is a Japanese philosophy that elevated the post-war economy from ruins within a few decades. The word "kaizen" translates to "continuous improvement" and encompasses the ongoing enhancement of oneself as a person and professional, the workplace, production processes, management, consumer relationships, and everything around.
To implement kaizen effectively in business, Japanese managers reinforce it with practical tools for optimizing workplaces, quality control, suggesting rational improvements, careful resource use, and more.
The Japanese Economic Miracle
The Japanese economic miracle refers to the unprecedented growth of Japan's economy from the mid-1950s to the oil crisis of 1973, averaging around 10% annually. Japan, previously known for producing low-quality, unusable products, transformed its reputation and became a competitor to leading American corporations.
The Japanese attribute their economic growth to kaizen as a way of thinking and approach to management. Interestingly, the ideas for improving product quality were initially introduced to Japan by Americans.
Origin and History of Kaizen
In 1946, America sent its best engineers to Japan to give lectures on quality and share their experiences with Japanese industrialists. In 1950, W. Edwards Deming, the founder of the modern quality movement, lectured in Japan. The Japanese so effectively implemented his ideas that 20-30 years later, American delegations visited Japan to learn from their experience.
W. Edwards Deming, an American scientist and co-author of the Shewhart-Deming cycle (PDCA), played a crucial role in Japan's economic revival. The term "kaizen" as a management concept became widely known in 1986 after the publication of Masaaki Imai's book "Kaizen: The Key to Japan's Competitive Success."
Key Principles of Kaizen Management
Customers
Customers are the most important link in the production chain, and all company efforts aim to provide them with quality products at a low price. It's essential to anticipate market demands and adjust production to meet new needs. Customer feedback is a crucial component of kaizen.
Employees
Employees are the company's most valuable asset, and kaizen is impossible without their support. In Japanese companies, the well-being of the enterprise equates to the well-being of the employees. Relationships with personnel are built on mutual interest in producing high-quality, competitive products.
Kaizen management includes five systems to establish relationships between individuals and the organization:
- Lifetime employment
- On-the-job training
- Job rotation
- System of virtues
- Reward system
Management
Kaizen favors leadership over formal authority. Japanese managers earn respect through their knowledge, experience, decisions, and personal example. They spend a lot of time on the production floor and freely communicate with employees at all levels.Implementing kaizen in a company is impossible without top management support. Improvement goals are set at the top level and cascaded down. Realizing the plans requires decision-making and investments. The higher a manager is in the hierarchy, the more improvement actions are expected.
Kaizen vs. Traditional Western Management
Aspect | Kaizen | Western Management |
Focus | Process | Result |
Development | Gradual, sometimes plus innovation | Leapfrogging, only through innovation |
Resource Use | Economical use | Non-rational use as long as there's profit |
Team Relations | Mutual help, support, knowledge sharing | Individualism, competition |
Leadership | Leader with authority and experience | Boss with power |
Ideal Environment | Slow economic growth with resource scarcity | Economic boom with abundant resources |
Perspective | Long-term | Short-term |
Goals of Kaizen
The Japanese adopted kaizen to combat post-war devastation. As a result, Japan not only recovered but also became a leading global producer of high-quality, competitive products, including automobiles, equipment, and electronics. This transformation happened despite the country's lack of resources, small territory, and relative isolation.
The primary goal of kaizen management is to satisfy consumer needs.
To achieve this, top management sets clear priorities for product quality, costs, and delivery discipline, cascading them throughout the enterprise.
Kaizen also aims to:
- Improve product quality while reducing costs
- Increase company profits
- Motivate staff and maximize their potential
- Maintain long-term market competitiveness
- Use limited and expensive resources efficiently
Applying Kaizen Methods
Kaizen is implemented through practical tools and methods, such as:Total Quality Management (TQM)
Total Quality Management is a management philosophy focused on improving product quality, reducing costs, and satisfying the needs of consumers and employees. It's the most crucial and extensive tool of kaizen.
Just-In-Time (JIT) Production System
Developed by Toyota's vice-president Taiichi Ohno in 1954, JIT ensures parts are supplied to the assembly line precisely on time and in the needed quantity. This approach eliminates the need for large inventories, improves quality, and speeds up assembly.
Total Productive Maintenance (TPM)
TPM involves every employee taking care of their equipment and workplace. This includes maintaining machines, anticipating potential breakdowns, and developing equipment operation standards.
Suggestion System
Adopted from the US, the suggestion system encourages employees to propose improvements individually or in small groups. This system supports kaizen and fosters a sense of involvement among workers.
Small Group Activities
Workers in small groups (6-10 people) within the workshop seek ways to improve processes and product quality, reduce downtime, and save materials. Quality Control Circles (QCC) are common small groups focusing on workplace improvements, safety, and productivity.
Kanban
Initially developed at Toyota, kanban uses cards attached to containers of parts that move along the assembly line. This system minimizes storage and communicates between production and storage workers.
Zero Defects (ZD)
Developed by Philip Crosby, ZD aims for no defects in production. This involves preventing defects rather than finding and correcting them, ensuring consumer receives defect-free products.
Advantages and Disadvantages of Kaizen
Advantages:
- Improved product quality with reduced costs
- Satisfied customers
- Efficient use of resources and equipment
- Atmosphere of mutual help and cooperation
- Motivated employees
Disadvantages:
- Requires investments that may not pay off immediately
- Long-term effects (3-5 years) to see results
- Not suitable for rapidly growing economies
- Challenging to engage employees at all levels
- Human factors like laziness, greed, and dishonesty can hinder implementation
Kaizen in Practice
Many Japanese corporations like Toyota, Mitsubishi, and Nissan support kaizen. Nestlé S.A. is an example of a Western company adopting kaizen principles.Nestlé
Nestlé, a Swiss multinational food and beverage company, has consistently been on the Fortune 500 list for 22 years. Lean manufacturing and the absence of waste are Nestlé's primary mission. Kaizen ideas are evident in Nestlé's Corporate Business Principles and Quality Policy.
Nestlé's top management commits to the highest quality and safety standards through:
- Fostering a quality culture to develop, produce, and deliver zero-defect products trusted by consumers
- Complying with applicable laws and international standards
- Continuously improving the quality management system
- Encouraging employee and partner participation in quality standards, training, and mentoring
To create value and earn consumer trust, Nestlé implements 4 principles:
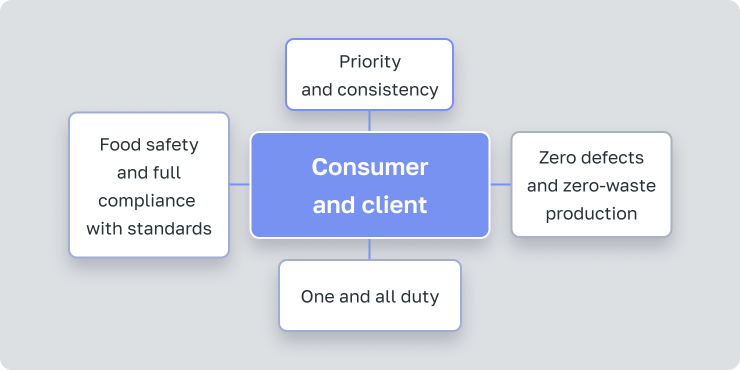
Total Quality Management (TQM): Definition and Essence
Total Quality Management (TQM) is closely linked to kaizen. Masaaki Imai describes TQM as "the main highway leading to kaizen," often equating the two concepts.
TQM involves systematic approaches and statistical methods to convert company problems into specific numbers, engaging top, middle management, and all employees in quality improvement activities across the entire enterprise.
Principles of TQM
Kaoru Ishikawa, a founder of the TQM movement, outlined six features of TQM in Japan:
- Company-wide application involving all employees
- Importance of education and training
- Quality Control Circles
- Regular TQM audits by top management or external organizations
- Use of statistical methods
- Government support for TQM
TQM contrasts sharply with traditional quality management approaches:
Traditional Quality Management | TQM |
Customer satisfaction | Satisfaction of consumers, employees, and society |
Actions to improve product quality | Actions to improve processes and systems quality |
Corrective actions on quality | Preventive actions on quality |
Quality management training only for quality control department employees | Quality management training for all employees |
Quality responsibility lies with the quality control department | Quality responsibility lies with all employees |
Solving urgent quality problems, "putting out fires" | Identifying and solving chronic problems |
Isolated problem-solving | Collaborative problem-solving |
Deming's 14 Points for Implementing TQM
W. Edwards Deming formulated a 14-point algorithm for implementing TQM:
- Ensure consistency of purpose towards improvement of products and services.
- Adopt the new philosophy.
- Cease dependence on inspection to achieve quality.
- End the practice of awarding business on price alone.
- Constantly improve every process for planning, production, and service.
- Institute on-the-job training.
- Adopt and institute leadership.
- Drive out fear.
- Break down barriers between staff areas.
- Eliminate slogans, exhortations, and targets for the workforce.
- Eliminate numerical quotas and numerical goals.
- Remove barriers to pride of workmanship.
- Institute a vigorous program of education and self-improvement for everyone.
- Involve everyone in the company in the transformation.
Advantages and Disadvantages of TQM
Advantages:
- Improved product quality
- Customer satisfaction and loyalty
- Reduced production costs
- Increased company profitability
- Adaptability to environmental changes
- Motivated employees through engagement
- Strengthened corporate culture
Disadvantages:
- Significant initial financial investments for personnel training and hiring quality consultants
- Time-consuming process to establish communication and form a new corporate culture
- Formalized production processes through new standards and rules
- Challenges in ensuring necessary employee engagement
- Lack of short-term effects
- Unsuitability for the service sector, small businesses, and non-profit organizations
TQM in Practice
An example of TQM in practice is the Indian company National Engineering Industries Limited (NEI), part of the CK Birla Group. In 2015, NEI received the Deming Prize for quality management.
NEI manufactures bearings for the automotive and railway industries under the NBC Bearings brand, exporting to 21 countries. The company adheres to the "Zero Defects" concept, currently aiming to reduce defects to 50 parts per million and eventually below 10 parts per million.
Kaizen in IT
Kaizen philosophy suits not only manufacturing enterprises but also IT development teams. Many modern agile methodologies are based on kaizen principles, such as:
- Scrum: Inspired by Japanese practices, Scrum incorporates kaizen principles like the PDCA cycle, continuous activity analysis, obstacle elimination, mutual support, and open information sharing.
- Lean: Lean development is an adaptation of lean manufacturing for IT, focusing on eliminating waste and fostering continuous learning, decision-making, and motivation.
- Kanban: Originally a tool of JIT, Kanban has been adapted for IT development, emphasizing existing methods' improvement, agreed changes, initiative encouragement, and clear role distribution.
Programs for Kaizen and TQM Implementation
Various project management services facilitate quality control and continuous improvement, such as Worksection.Worksection
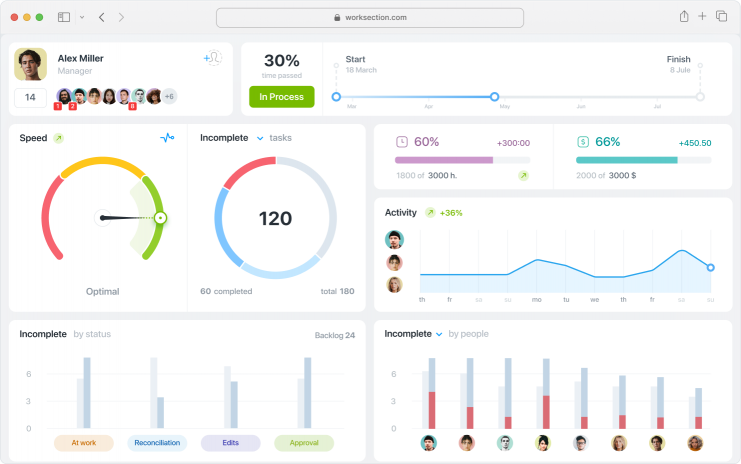
Worksection is a SaaS service that ensures transparent communication between management and teams, clients, and freelancers. It supports kaizen and TQM with features like:
- Task commenting, assignment, and client visibility without internal details
- Setting deadlines and budgets for each task, with expense control and adjustment
- Adding checklists, files, labels, and statuses to tasks
- Real-time communication in a task context
- Gantt charts for task progress visualization
- Reports on team workload
Conclusion
Kaizen is a fantastic philosophy for life and business, an evident path to societal well-being. This simple idea of continuous improvement demands deep transformations in thinking, relationships, and production processes, which not everyone is ready for.While some Western companies have abandoned kaizen tools as inefficient and outdated due to bureaucracy, worker neglect, and process opacity, kaizen principles thrive in the IT industry. They form the foundation of many agile methodologies and help create high-quality software products in a short time.