Шість Сигм - це поняття з теорії ймовірності, виражене формулою: не більше 3,4 дефектів на мільйон продукції або процесів. Математична задача методології - зменшити розсіювання варіантів.
Тобто, в буквальному сенсі 6 сигм - це методологія управління проектами, орієнтована на виключення браку виробництва як клас.
Принципи
- Зробіть процеси передбачуваними
- Постарайтеся так, щоб виробничі і бізнес-процеси можна було описати, виміряти, аналізувати, покращувати і контролювати
- Щоб домогтися успіху за допомогою Шести сигм, задійте весь персонал організації, особливо топ-менеджмент
- Ставте конкретні цілі, які можна підрахувати або виміряти: знизити витрати на 20%, підняти прибутковість на третину, зменшити виробничий цикл на годину
- Залучайте менеджерів з сильними лідерськими якостями і вмінням чути партнерів
- Краще приймайте рішення на основі підтвердженої інформації та статистики, ніж керуючись припущеннями.
Алгоритми
Шість сигм пропонує два підходи в залежності від того, покращуєте ви процес - DMAIC, чи створюєте новий продукт - DMADV, він же DFSS. Обидва методи можна описати формулою Плануй-Роби-Перевір-Виправ.
Алгоритм DMAIC
- Визначте цілі проекту і потреби покупців. Сформуйте команду проекту, встановіть її зону відповідальності і розподіліть повноваження.
- Зберіть поточні дані, «виміряйте» ключові параметри процесу.
- Проаналізуйте зібрану інформацію і виявить фактори, які впливають на якість роботи організації або бізнес-діяльність. Знайдіть головну причину браку і дефектів, запропонуйте методи, як їх усунути.
- Поліпшіть або оптимізуйте поточні процеси. Зробіть пробні зміни.
- Контролюйте ваші правки, щоб будь-які відхилення від мети знову не вилилися в дефекти. Повідомляйте про хід проекту на інформаційних стендах, стежте, як працюють зі статистикою. Повторюйте процес, поки не досягнете необхідної якості.
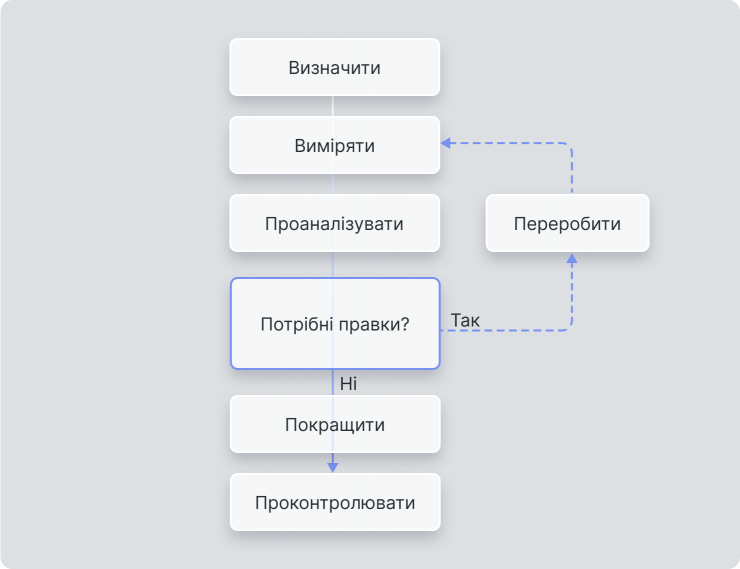
Алгоритм DMAIC
Головний принцип DMAIC - діяти на випередження. Нові переваги споживачів потрібно спрогнозувати, дефекти - попередити.
Алгоритм DMADV або DFSS
1 Визначте цілі, які повинні збігатися з бажаннями покупців і стратегією підприємства. Створіть команду проекту.
2 Позначте основні характеристики продукту, потреби для виробничого циклу.
3 Знайдіть і проаналізуйте кілька варіантів.
4 Виберіть кращий варіант і почніть над ним працювати.
5 Реалізуйте проект на практиці.
Інструменти
Використовувати можна як принции менеджмента якістю, так і статистичні методи. До перших відносяться:
- «5 чому». Ставимо це питання до тих пір, поки не з'ясуємо головну причину дефектів
- Карта бізнес-процесів. Схематично зображуємо, які ресурси у нас є і що має бути зроблено. Наприклад, ось карта процесів при замовленні і відправлення товару:
- Аналіз витрат і вигоди. Коли є кілька варіантів проекту, то виберіть той, у якого співвідношення вигоди до витрат найкраще.
- «Дерево» показників, критично важливих для якості (CTQ tree). Намалюйте схему з ключовими характеристиками для вашого проекту. Наприклад, ось «дерево» для створення магазину дитячого одягу.
- Плаування експерименту. Допомагає ефективніше проводити дослідження і підготуватися до дослідів.
До статистичних інструментів відносяться:
1 Дисперсійний аналіз
2 Регресійний аналіз
3 Точкова діаграма
4 Контрольна карта
5 Крива Парето.
Ієрархія
Концепція управління нагадує східні бойові мистецтва. Роль виконавця залежить від його пояса - рівня знань і навичок Шість Сигм.
- На вершині піраміди знаходиться Головне керівництво. Воно розподіляє обов'язки і ресурси. Головне керівництво усуває внутрішньокорпоративні бар'єри і бореться з природженим опором персоналу до змін.
- Чемпіони впроваджують методологію в організації і наставляє володарів Чорних поясів.
- Майстри чорного пояса контролюють впровадження Шести Сигм і командують звичайними Чорними поясами.
- Чорні пояси під наглядом майстрів займаються проектом і виконують доручені їм завдання;
- Зелені пояси - це персонал, який крім своїх обов'язків працює над впровадженням методології. Стежать за цим Чорні пояси.
- Іноді виділяють Білі пояси і Жовті пояси - співробітники компанії, які знають Six Sigma на початковому рівні і або частково беруть участь в проекті, або стежать за діями досвідчених колег.
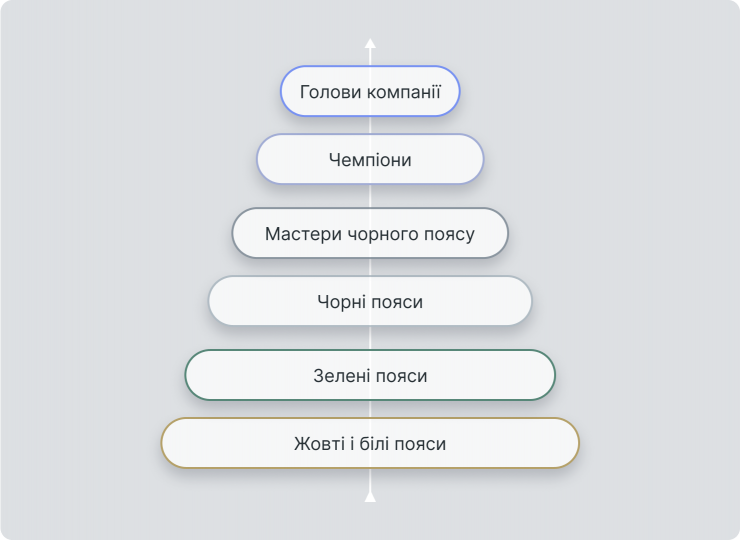
Ієрархія Шести Сигм
Пройти сертифікацію можна в компаніях ASQ і IISE. Навчання проходить як на місці в США, так і онлайн. Скласти іспити також можна зі свого комп'ютера, встановивши спеціальне програмне забезпечення.
Сертифікати видає також розробник методології, компанія Motorola. Навчальні курси проходять не тільки в Північній Америці, але і в Європі, Азії, Африці.
Відмінності від схожих методологій
З кінця 2000-х рр. стала популярною Lean Six Sigma методологія - поєднання підходів Lean, ощадливого виробництва, і Шести Сигм. Завданням Lean є скорочення витрат і прощання з робочими процесами, які не несуть цінності для споживача. Вона також допомагає стандартизувати виробництво.
Методологія Six Sigma націлена на зменшення дефектів і вимагає посиленого контролю за процесами. Шість Сигм з її статистичним аналізом - практично технічна дисципліна в порівнянні з Lean, де більше задіюють візуальний контроль і змінюють організацію робочого місця.
Шість Сигм і Lean порівнюють зі ще однією методологією (для багатьох це швидше корпоративна філософія) - Кайдзен. Вона також вимагає від організації безперервного поліпшення і стандартизації процесів. Однак головна відмінність Кайдзен - наголос на швидкі і прості рішення, які обговорюються відкрито при персоналі.
Недоліки
1 Все більше організацій почали тренувати майбутніх володарів Чорних поясів. В результаті, як вважають критики, впала якість сертифікації. Чорні пояси випускаються з меншими знаннями.
2 Журнал Fortune стверджував, що майже всі з 58 великих компаній, які заявили про вірність Шести сигмам, потім випали з індексу S & P 500. Методологія Шість сигм, наполягають журналісти ділового видання, не допомагає створювати проривні продукти і технології.
3 Це може бути пов'язано з іншим недоліком, який приписують Six Sigma - обмеження творчої свободи. Згідно такої думки, постійні «виміри» і статистичний аналіз не дають проектній команді зайнятися брейнштормінгом і придумати несподівану ідею. Методологія має строгий алгоритм і переслідує, перш за все, комерційні цілі, а не інноваційні.
4 Заточеність Шести Сигм на статистиці також є предметом критики. Теоретичні суперечки вирують навколо деяких інструментів, які можуть не до кінця враховувати ризики.
Що таке шість сигм в управлінні часом?
Методологія Six Sigma виділяє два часи - провідний і час циклу.- Провідний час говорить про те, скільки пройшло з моменту запиту клієнта і отримання ним товару/послуги.
- Час циклу означає кількість годин, яка йде на повний виробничий цикл або роботу над процесом.
1 стадія - Знайомство з проектом
2 стадія - Збір даних
В ході аналізу даних Чорні пояси знайшли такі дефекти:
- Персонал не сформулював точно, що варто враховувати в провідному часі. Наприклад, чи включати туди перерви на обід і святкові дні.
- Покупці часто направляли заявку в неробочий час, що не відстежувалося системою. Виявилося, що лічильник не фіксував деякі підготовчі процеси, і провідний час в компанії триває ще довше, ніж 50,1 годин.
Ці труднощі з психологією вирішились, коли ПМ стали регулярно спілкуватися з керівництвом і персоналом, щоб разом працювати над новими ідеями.
3 стадія - Аналіз
ПМ використовували діаграму Ісікави, аналіз видів і наслідків відмов і метод Six Sigma «5 Чому», щоб виділити можливі дефекти:
- Між робочими процесами занадто багато затримок
- Деякі процеси тривають занадто довго, збільшуючи провідний час в цілому
- Запити клієнтів надходять поза робочим часом, і можуть бути оброблені пізніше, ніж з початку наступного дня
- Одна заявка вимагає кілька різних процесів, що збільшує провідний час в цій ситуації
- Інформація з бази даних надходить в різних файлових форматах, і деякі з них важко обробити
- Окремі запити не вписуються в стандартний протокол і вимагають особистого втручання IT-відділу
- Співробітники «розкидають» отримані заявки і не вирішують їх відразу.
4 і 5 стадії - Поліпшення і контроль
ПМ перевірили кожен з можливих дефектів і прийшли до висновку, що ключовою проблемою є довгі інтервали між робочими процесами. Більше того, час між операціями перевищував час, який витрачався на роботу.Тому ПМ перерозподілили обов'язки, щоб один співробітник міг виконувати тепер кілька процесів, а не чекати, поки його колега впорається зі своїм завданням. Такий захід поліпшив організаційну гнучкість і послабив монотонність робочого процесу.
ПМ представили пілотний проект керівництву і персоналу. Після зауважень і побажань співробітників в план внесли поправки. Виконавці пройшли додаткові тренування, перш ніж лічильники включили знову. Проект вийшов успішним: провідний час тепер тривав 23 години.
Що таке шість сигм в промисловості
Врятувати ситуацію повинна була six sigma методологія, а саме алгоритм DMAIC. Виробничий процес проходив в 3 стадії:
1 Підготовчий етап. Склу надавали потрібну форму, після чого шліфували краї, мили, висушували, інспектували.
2 Друк. На поверхню скла наносилися спеціальне чорнило, яке потім висушували в відсіках печі. Таке покриття захищає від сонячних променів.
3 Загартовування і обробка. Скло нагрівають до потрібної температури, згинають до заданої форми і охолоджують потоком повітря високого тиску. Після чого його оглядають і відправляють на продаж.
1 стадія - Знайомство з проектом
Виробничий брак почався з придбанням універсальної печі, на чому наполягала материнська компанія. Нове обладнання повинно було робити скло як для бічних, так і задніх дверей автомобіля. Однак задні скла виходили набагато дефектнішими, ніж очікувалося, і не завжди влаштовували якістю споживачів.
Три стадії виробничого процесу виходили з таким відсотком браку:
Підготовчий етап - 1,5%
Друк - 1,5%
Загартовування і обробка - 10,5%.
Менеджмент компанії очікував ці показники на рівні 0,5% для перших двох стадій і 6,5% для останньої.
Проектна команда зробила схему, в якій виробництво розділили на дрібні процеси, і виявила такі дефекти:
Процес | Дефект | Опис | |
Підготовчий етап | Дефект1 | Відламані уламки | Від країв відшаровується крихта |
Дефект2 | Стружка | Краї зрізаються при контакті зі шліфувальним колесом | |
Друк | Дефект1 | Неправильний друк | На поверхні частково немає чорнила |
Дефект2 | «Запорошена відмітка» | Частинки пилу потрапили на надруковану поверхню | |
Загартовування і обробка | Дефект1 | Відбиток від котушки печі | На склі залишилися сторонні частинки |
Дефект2 | Руйнування від повітряного потоку | Скло поламалося на дрібні осколки під час остужування повітрям з високим тиском | |
Дефект3 | Неправильний вигин | Скло не догнули до потрібної форми |
2 стадія — Збір даних
ПМ склали матрицю причин і наслідків, щоб виявити залежності між виробничими процесами і випуском. У ній виставляються 3 оцінки: 1 - слабка кореляція, 3 - середня кореляція, і 9 - висока кореляція.Виявилося, що під час загартовування і обробки, найбільш проблемної стадії, дефекти можуть бути пов'язані з температурою в кожному з 4 відсіків печі, температурою скла і швидкістю роботи печі.
3 стадія - Аналіз
Як і попереджала матриця причин і наслідків, під час загартовування і обробки брак виникав через відхилення в температурі печі і скла, а також через швидкість виробничої лінії.
На підготовчому етапі дефекти виникали внаслідок зайвого тиску на матеріал, неправильної фіксації і надмірної сили ріжучого обладнання. Під час друку проблеми викликалися через непросохлі плівки, дуже суху температуру, завантаження форми в верстат «задом наперед» і недостатньо щільні роздільники скла.
4 стадія - Поліпшення
ПМ провела планування експериментів. Для кожної стадії виробничого процесу підібрали особливий комплекс.Для підготовчого етапу підготували 16 нових рішень. ПМ експериментували з налаштуванням ріжучого спорядження і параметрами фіксації. В результаті ступінь браку впала до бажаної 0,5%.
На стадії друку проектна команда провела експерименти з товщиною роздільників і температурою. В результаті відсоток дефектності також знизили до 0,5%.
Під час загартовування і обробки ПМ провели 400 ітерацій для кожного з 16 варіантів, щоб досягти покращених показників. Команда знайшла оптимальну температуру для кожного з відсіків печі і правильну швидкість виробничої лінії.
Тепер ступінь браку впала до 3%, що виявилося навіть краще поставленої мети - 6,5%.
5 стадія - Контроль
Зниження дефектності ще належало закріпити. ПМ склали контрольний план, в якому вказали необхідні параметри для печі і виробничої лінії. Також вони розподілили, хто буде моніторити процеси, як часто це робити, і які вимірювальні прилади для цього використовувати.Застосування великими компаніями
Після цього методологію впровадили велика кількість важковаговиків промислової і фінансової сфери. Автовиробник Ford завдяки Шести Сигм збільшив виручку в 2000-му році на $ 300 млн. Компанія витратила кілька мільйонів на навчання персоналу методології і не пошкодувала. ПМ створили ряд успішних проектів, які сподобалися клієнтам Ford.
General Electric - одна з перших компаній, яка використовувала розробку Motorola. Виконавчий директор Джек Уелч почав навчати персонал премудростям Шести Сигм в 1995 році. Протягом 13 днів і 100 годин менеджери проходили насичену програму. Зелений пояс став вимогою для підвищення, а успішне впровадження методології збільшувало премію на 40%. Головне керівництво нерідко приходило на лекції, щоб особисто відповісти на питання персоналу.
Третій найбільший банк США Bank of America використовував в 2005 році принципи Six Sigma, щоб зменшити час, який було потрібно для відкриття інтернет-рахунків. Кількість кроків клієнтів знизилося з 10 до 4. Користувачам стало простіше авторизуватися, у них з'явилася текстова онлайн-підтримка. В результаті різко зросла кількість кредитів і депозитів, а банк збільшив прибуток на 30%.
Авіавиробник Boeing в 1999 році запустив масштабне навчання персоналу принципам Шести Сигм. Компанія випустила близько 60 Черних поясів і понад 300 Зелених поясів. Через 5 років Boeing знизила витрати на $ 210 млн.
У 2007 році 82 з 100 найбільших організацій США впроваджували принципи Six Sigma. Багато з них були лідерами у своїй галузі і на міжнародному рівні. Ось дослідження, в якому доведено, що протягом 4 років впровадження компанії отримували додатково 1-7% від прибутку.
ТОП компаній та їх прибутки з Six Sigma
Рік запуску Six Sigma | Компанія | Тип бизнесу | Виручка в 2008 р., $млн | Кількість робітників |
1986 | Motorola | Виробництво мобільних телефонів | 30 146 | 64 000 |
2001 | Bechtel | Будівництво, управління проектами | 31 400 | 44 000 |
1998 | Honeywell | Автоматизація та управління | 36 556 | 128 000 |
2001 | Caterpillar | Виробниче обладнання | 51 324 | 112 887 |
1999 | Dow Chemicals | Хімічна промисловість | 57 514 | 46 102 |
1999 | McKesson | Фармацевтика | 106 600 | Невідомо |
2001 | Bank of America | Банківська сфера | 119 643 | 243 000 |
2000 | Ford Motor Co. | Виробництво авто | 146 277 | 213 000 |
1995 | General Electric | Виробництво техніки | 182 515 | 323 000 |
ТОП компаній та їх економія с Six Sigma
Компанія | Період спостереження | Сумарна виручка за період спостереження, $млн | Зекономлена сума, $млн | Зекономлена сума, % від виручки |
McKesson | 1999-2002 | 158 773 | 40 | 0,03 |
Ford Motor Co | 2000-2003 | 698 970 | 1700 | 0,3 |
Caterpillar | 2001-2002 | 20 450 | 138 | 0,7 |
General Electric | 1995-2002 | 839 599 | 8000 | 1 |
Bank of America | 2001-2004 | 158 267 | 2000 | 1,3 |
Dow Chemicals | 1999-2002 | 119 613 | 1500 | 1,3 |
Bechtel | 2001-2003 | 41 359 | 625 | 1,5 |
Honeywell | 2000-2002 | 72 300 | 1800 | 2,5 |
Motorola | 1986-2004 | 400 695 | 17000 | 4,2 |
Книги
Solving Complex Industrial Problems Without Statistics (Рішення складних промислових задач без використання статистики) / Ральф Полак, 2016 рік
Книга для тих адептів Шести Сигм, які не особливо сильні в математичній частині методології. Замість цього автор пропонує 14 практичних прикладів, де вчить «якісному мисленню». Полак розкриває, як швидко розрізнити поганий випуск продукції від хорошого, як візуально знайти «докази», які приведуть до причин дефектів. Ставтеся до якісного аналізу як до огляду місця злочину, напучує нас автор.Шлях Шість Сигм. Практичний посібник для команд впровадження "/ Піт С. ПЕНД, Роберт П. Ньюман, Роланд Р. Кевенег, 2005
Бережливе виробництво + шість сигм / Майкл Л. Джордж, 2007
Шість сигм для чайників / Крейг Джіджі, 2008
Додатки та програми
Worksection
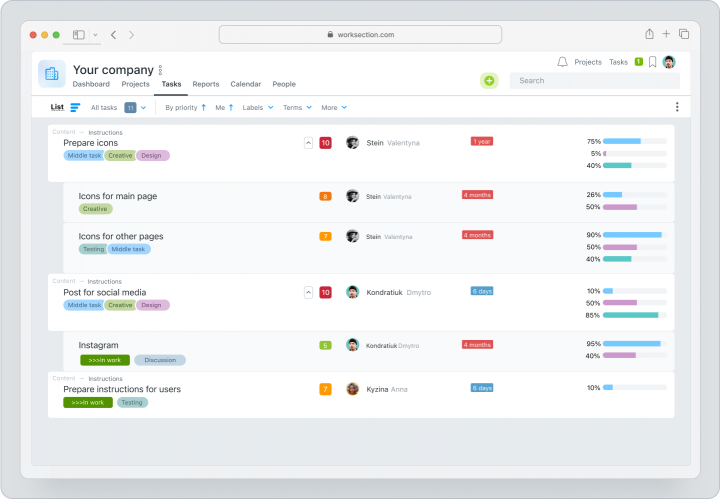
З Worksection зручно стежити за активністю команди і прогресом всього проекту. Використовуйте інструменти Six Sigma:
- прописуйте плани покращень в задачах чек-лістами або підзадачами
- відзначайте відповідальних за модернізацію, моніторте прогрес і завершення в реальному часі