Today on the Worksection blog, we will explore the concept of a bottleneck and its role in optimizing enterprise workflows.
The term "bottleneck", also known as a "narrow place", is a central element of Eliyahu Goldratt's Theory of Constraints (TOC) and a key pillar of lean manufacturing.
The Theory of Constraints, formulated in the 1980s, focuses on managing production enterprises. The essence is that every production system has constraints that hinder efficiency. Eliminating the primary constraint will significantly improve system performance more than attempting to impact the entire system at once. Therefore, the process of improving production should start with eliminating bottlenecks.
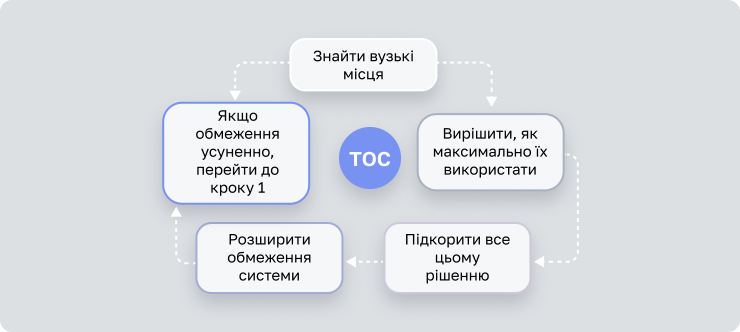
The Five Focusing Steps of the Theory of Constraints by E. Goldratt
Nowadays, the term bottleneck can be used for managing team tasks in any industry, including services, software development, logistics, and daily life.
What is a Bottleneck?
A bottleneck is defined as a point in a production system where an overload occurs because materials flow in too quickly to be processed at the same rate. It is often a station with lower capacity than the preceding node. The term comes from the analogy of a bottle's narrow neck, which slows the liquid's flow.
In production, bottlenecks cause delays and increased production costs, reducing overall efficiency and increasing delivery times to customers.
There are two types of bottlenecks:
- Short-term bottlenecks are caused by temporary issues, such as a key employee's sick leave or vacation.
- Long-term bottlenecks are persistent, like a single person being responsible for processing a large volume of information at the end of each month.
Identifying Bottlenecks in the Production Process
Several methods can identify bottlenecks in production, ranging from simple observation to complex tools.Queues and Backlogs
Processes that accumulate the most significant backlog of work-in-progress units typically indicate a bottleneck.
Throughput
The throughput of the entire production line is directly affected by the output of the bottleneck equipment.
Full Capacity
Monitoring the utilization percentage of each piece of equipment can help identify bottlenecks. The equipment operating at maximum capacity is usually the bottleneck.
Waiting Times
Observing idle times can reveal bottlenecks, as equipment following a bottleneck often experiences long downtimes.
Tools for Identifying Bottlenecks
Value Stream Mapping (VSM)
- Visualizes where waiting times and excess inventories occur in the process.
Yamazumi Chart
- A bar chart showing each operator's total repeatable working time, helping to evaluate and balance workload.
Step Capacity Histogram
- A simple histogram comparing the capacity of each production step, clearly highlighting bottlenecks.
Consequences of Bottlenecks
Bottlenecks limit production efficiency, leading to increased costs and missed profits. The negative effects include production delays, idle time, increased product costs, and worker demotivation.Managing Bottlenecks
Identifying the Problem
Bottlenecks can result from cumulative effects or be tied to a single process component.
Five Whys Technique
Ask "why" five times to trace the root cause of the bottleneck.
Action Steps
Once identified, determine actions to alleviate the bottleneck, such as reallocating employees, adjusting schedules, or upgrading equipment.
Reducing the Impact of Bottlenecks
Three approaches can help:
Increase Capacity
- Add resources, ensure continuous material supply, focus on quality, and improve scheduling.
Sell Excess Production
- Find subcontractors interested in excess production capabilities.
Reduce Unused Capacity
- Sell off equipment with excess capacity and reallocate or reduce personnel.
Examples of Bottlenecks Beyond Production
- Transportation: Traffic jams.
- Computer Networks: Slow WiFi routers.
- Communication: Overloaded developers.
- Software: Slow code elements.
- Computer Hardware: Limited CPU performance.
- Bureaucracy: Lack of necessary forms or limited operating hours.