Мало кто не слышал о Lean Manufacturing/ Lean Production/ Lean Enterprise — бережливом производстве (товаров, услуг и пр.). Термин Muri (Мури) в этой, без преувеличения, философии обозначает перегрузку, от которой лучше избавиться сразу, пока она не стала критической. Но так ли просто это сделать, чтобы ничего не потерять в итоге?
Подробности: что такое Мури?
Мури — необоснованная перегрузка персонала (операторов), техники и прочих факторов производства. Чаще всего это явление возникает из-за производственных процессов, которые не оптимизированы должным образом, что ведет к чередованию периодов простоя с периодами слишком интенсивной работы в стрессовом режиме. Иногда — даже с авариями, сбоями.
Разумеется, на пользу делу это не идет:
Когда у нас не остается энергетических резервов, мы склонны действовать опрометчиво.
Джефф Сазерленд,
один из разработчиков методологии Scrum
Непродуманные и, как следствие, непродуктивные действия команды — причина малопродуктивной работы:
Большинство бизнес-процессов на 90 % состоят из потерь и лишь на 10 % из работы, добавляющей ценность.
Джеффри Лайкер,
профессор промышленного и операционного инжиниринга в Университете Мичигана; президент Liker Lean Advisors, автор бестселлера «Дао Тойота», «Путь Тойота к Лин-лидерству»
Итак, избыток Мури — прямой путь к потерям или отходам (их называют Муда).
Избавившись от Мури, можно заметить, что значительная часть отходов исчезла автоматически, упростив этим жизнь всем участникам производственного процесса.
Примеры Мури
Чтобы лучше понять природу данного вида потерь, рассмотрим его на примерах:
- начало работы без должного предварительного обучения;
- плохо оснащенные рабочие места, отсутствие нужных инструментов, оборудования;
- нечеткие инструкции;
- колеблющийся спрос на производимый продукт;
- отсутствие квалифицированного технического обслуживания, технической поддержки;
- недостаточно надежные и не проверенные технологии, процессы;
- не налаженные коммуникации между участниками процесса.
Из приведенного выше списка видно, что Мури охватывает множество процессов как в производственных, так и в сервисных компаниях, приводит к проблемам и отходам разного рода.
Зачастую мы не справляемся с этими отходами, пытаясь сконцентрироваться на уменьшении времени, необходимого для выполнения отдельных задач, «тасуя» те или иные факторы, требуя экономии ресурсов.
Фактически же все это ведет к тому, что оператор и оборудование работают более интенсивно, не принося реальной выгоды процессу.
Получается, что
Мури — потери, вызванные недостаточно разумным обращением с имеющимися ресурсами, работа на износ.
Очень хорошо это иллюстрирует следующее высказывание:
Команда, которой для того, чтобы уложиться в сроки, регулярно требуется проявлять героизм, работает не так, как следовало бы.
Джефф Сазерленд, один из разработчиков методологии Scrum
Если же проблема Мури ликвидирована, то команда будет работать намного эффективнее, в условиях минимального стресса.
Как ликвидировать или минимизировать Мури?
Существует множество Lean Manufacturing Tools (инструментов бережливого производства), созданных специально для уменьшения Мури в управлении проектами. Конечно, постоянно нужно использовать элементарный здравый смысл, не опираясь только на жесткую методологию, а выбирая то, что пойдет на пользу и вашим работникам, и вашим клиентам.
Методология 5S
Чрезвычайно простая, но от этого не менее эффективная методология, позволяющая решить широкий круг задач в любом рабочем пространстве. При помощи 5S можно устранить необоснованные движения и стресс, обеспечив нахождение каждого нужного элемента на оптимальном с точки зрения производства и эргономики месте.
Кроме того, 5S — гарантия того, что стандарты контроля ясны, и отклонение от них является очевидным и требующим немедленного исправления.Составляющие методологии 5S
- Сортировка. Рабочее место должно быть обязательно освобождено от всего, что не нужно для выполнения текущих задач. Как показывает практика, то, что оставлено под рукой на случай «а вдруг пригодится» — балласт, который становится источником возникновения хаоса и неразберихи. Все предметы труда, не использующиеся более 30 дней — кандидаты на удаление (или перемещение туда, где не мешают решать имеющиеся задачи).
- Соблюдение порядка. Все используемое для работы, должно быть расположено рационально и удобно. При этом следует учесть возникновение ситуации, когда задачу надо кому-либо передать. Преемник должен без труда найти все, что ему понадобится. Это сводит к минимуму рабочее время, которое тратится на бесполезные поиски.
- Содержание в чистоте. Рабочее место должно выглядеть презентабельно и убираться регулярно. Это позволит выявить потенциальные проблемы еще до того, как они помешают производству.
- Совершенствование. То есть системное соблюдение принципов, описанных выше.
- Стандартизация. Должен быть составлен чек-лист, по которому можно контролировать качество выполнения задач и своевременно корректировать недочеты. Все пункты должны быть понятны каждому сотруднику.
Польза стандартизирования и документирования всех процессов очевидно. Создавать инструкции могут и сами сотрудники при помощи любых камер и текстовых редакторов. Это станет гарантией того, что наиболее эффективные способы достижения тех или иных целей будут зафиксированы и переданы всем заинтересованным сотрудникам.
Что почитать:
Методология Total Productive Maintenance
Total Productive Maintenance (ТРМ, всеобщий уход за оборудованием) — еще один инструмент бережливого производства, который обязательно надо использовать для искоренения Мури.
Сколько раз вам приходилось менять планы, срывать сроки и разрабатывать новые решения из-за ненадежности оборудования?Использование ТРМ — оптимальный вариант избавления от проблем, спровоцированных неполадками с оборудованием.
Основная идея ТРМ — то, что работать с оборудованием должны не только технические специалисты, но и все, кто с ним связан (менеджеры, администраторы, руководители, программисты и пр.). На первый план выходит раннее выявление дефектов в оборудовании, которые впоследствии могут привести к серьезным сбоям в решении задач.
Направления внедрения ТРМ:
- модернизация оборудования;
- организация обслуживания оборудования тем, кто на нем работает;
- составление плана централизованного обслуживания оборудования;
- постоянное повышение квалификации всех, кто участвует в работе с оборудованием;
- оптимизация системы использования оборудования для изготовления тех или иных продуктов в зависимости от мощности оборудования и ресурсоемкости продукта;
- поддержание оптимальных условий для эксплуатации оборудования;
- взаимная поддержка в производственном процессе между всеми подразделениями;
- создание безопасных условий труда.
Что почитать:
Методология Дзидока (автономия)
Один из инструментов, о которых часто забывают. Его еще называют автоматизаций с человеческим прикосновением.
Обычно многие машины в той или иной мере оснащены датчиками контроля, но для процесса целиком эта методология применяется крайне редко.
Рациональное использование данного принципа позволяет во многом устранить неполадки, вызванные человеческим фактором (усталость, притупление внимания). Результатом становится значительная экономия ресурсов. Даже при том, что компания что-то теряет, остановив производственный процесс, все равно эти потери куда меньше, чем те, что последуют за выпуском бракованной продукции или, например, работы ПО, в котором по каким-то причинам произошел сбой.
Что почитать:
Методология SMED
Простой процесс, который тесно связан с 5S и ТРМ, но концентрируется на настройках оборудования. По сути, самый очевидный пример использования SMED — Pit Stop на гонках Формула-1.
Время, затраченное на наладку оборудования с точки зрения бережливого производства — потери. Ведь ничего не производится, а время идет.
Чтобы использовать рабочее время рационально, стоит воспользоваться таким алгоритмом внедрения SMED.
Что почитать:
- Быстрая переналадка: революционная технология оптимизации производства, Сигео Синго.
Практика: компании, которые успешно справились с Мури
Компания | Что использовали | Описание опыта |
Oriflame Cosmetics | 5s | Большинство элементов визуализации (разметки, различные сигналы) построены так, что даже новый сотрудник без труда поймет их смысл. Так, напольная разметка помогает поддерживать порядок возле рабочих зон конвейера, она показывает, где место тех или иных материалов, а где их ставить запрещено. С помощью вспомогательных знаков (фотографий, трафаретных изображений) можно точно указать, как должно стоять оборудование или какой тип материала должен быть на конкретном месте. Это сокращает время на поиск оборудования и материалов, упрощает подготовку новичков. С помощью переносных табличек можно управлять потоками продукции на ограниченном пространстве, что бывает очень полезно на небольших складах. |
ОАО «Хлебпром» | 5s | Для начала — наведение порядка. Отметили оборудование и материалы красным маркером, которые не использовали на протяжении месяца. Оказалось, что требовались лишь 4 из 15 тележек, ненужные из них направили на склад. |
Heineken | ТРМ | Начиная с октября 2004 года, ТРМ начал внедряться на предприятиях концерна по всему миру |
Boeing | 5s+ТРМ | Применение особой формы организации рабочего процесса, ограниченного одним подразделением, в котором располагалось всё обрабатывающее оборудование, сборочная лента и отдел по проверке качества продукта. Помимо этого, всё оборудование было выстроено в нужном для сборки порядке, и по возможности, оборудовано колесами для обеспечения мобильности, чтобы минимизировать нужду в лишних погрузчиках. Более того, каждое такое подразделение было обустроено небольшими складами для исключения ненужной транспортировки. |
Вердикт
Избавлять от Мури можно и нужно компаниям, которые работают в самых разных сферах. Эффект будет заметен достаточно быстро, главное, помните, что залог успеха использования Lean Manufacturing Tools — последовательность и постоянство:
Во многих эффективно работающих американских компаниях с уважением относятся к людям, внедряются кайдзен и другие инструменты TPS. Но нельзя забывать, что все эти составляющие должны работать как единая система. Их нужно применять в работе цеха изо дня в день, не авралами, а постоянно и последовательно.
Фудзио Тё, президент Toyota Motor Corporation
Один из вариантов облегчения задачи по избавлению от Мури — регулярный ответ на такие вопросы:
- Что было сделано вчера, чтобы избавиться от Мури?
- Что будет сделано сегодня?
- Какие проблемы встретились в ходе ликвидации Мури?
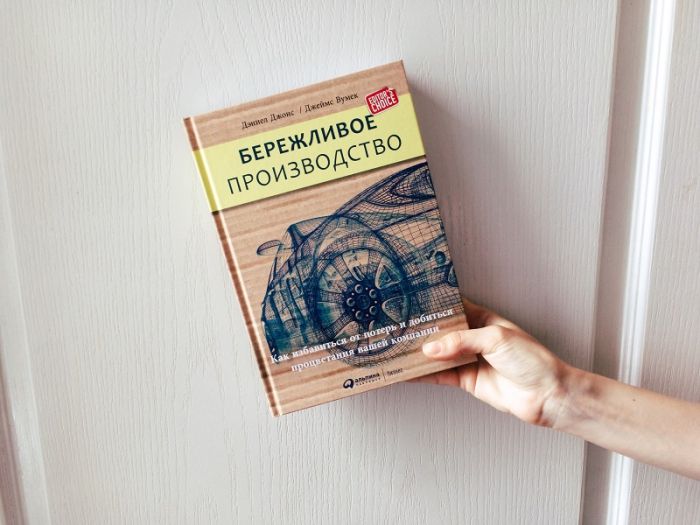