Бережливое производство (Lean) — одна из «долгоиграющих» концепций управления отдельными проектами и предприятиями. Её основы были заложены в первой половине XX ст. крупнейшим автомобильным предприятием того времени — Toyota. А SMED один из инструментов такого подхода к проектному менеджменту.
В рамках lean-production функционирует десяток методов и инструментов, которые в комплексе с программой управления проектами позволяют достичь высокой эффективности рабочего процесса.
Бережливое производство в той или иной форме используется в международных (Oriflame Cosmetics, Toyota) и национальных (украинские «УПЭК», «ТБМ») компаниях.
История бережливого производства
Противостояние — вот настоящий двигатель прогресса. Благодаря негласной борьбе между двумя автогигантами, Ford и Toyota, были заложены основы lean production.
В 1913 году Генри Форд создал первую в мире модель производственного потока. Обрабатываемое изделие передвигалось по конвейеру от одного рабочего процесса к другому, и в итоге превращалось в Ford Model T, вошедший в десятку автомобилей, изменивших мир по версии журнала Forbes. Использование автоматизации снизило себестоимость машины и позволило обеспечить серийный миллионный выпуск.
Тем не менее, у модели организации производства Форда было ровно два недостатка:
- отсутствие разнообразия продукции — заводы были заточены на выпуск одной модели в одном цветовом решении и спецификации.
- ограниченность пропускной способности — серийное производство требовало непрерывного выпуска изделий, и чем сильнее росли объемы, тем больше становились задержки между отправкой изделия на следующий рабочий процесс.
Спустя 26 лет после выпуска Model T в продажу, в Японии провели перепрофилирование Toyota. Вместо текстиля концерн стал выпускать автомобили. Основатель Toyota Motor Corp, Киширо Тойдода главным в борьбе за качество определил детальное изучение каждой стадии производственного процесса. Отчасти благодаря этому компании удалось выиграть первый тендер в 1936 г. на производство грузовиков.
Развить идею до крепкой концепции помешала Вторая мировая война. Toyota нуждалась в кардинально новом решении, так как послевоенная экономика Японии пребывала в катастрофическом положении. Около 40% национальных промышленных заводов и инфраструктуры были разрушены, и уровень производства упал до значений начала 30-ых гг.
Тайити Оно, ставший директором Toyota в 1950 г., решил позаимствовать опыт США. В штатах он и познакомился с одним из чудес «американской мечты» — супермаркетами, в которых запасы пополнялись по мере необходимости. Посетил директор и заводы Генри Форда. По возвращению на родину Тайити Оно вместе с Сигео Синго решили поставить во главу угла стратегию вытягивания (производство согласно реальному спросу), а не выталкивания (производство — на планируемых объемах продаж).
Комплекс методов реализации стратегии получил название Toyota Production System — TPS, и стал прообразом Lean Production. Само понятие «бережливое производство» ввела в обиход книга Машина, которая изменила мир Дж. Вумека и Д. Джонса.
Рекомендуем почитать их книгу Бережливое производство. Как избавиться от потерь и добиться процветания вашей компании.
Методы бережливого производства
SMED, о котором пойдёт речь сегодня, важный, но не единственный инструмент воплощения бережливого производства.
В концепции Lean Manufactoring выделяют такие методы:
- поток единичных изделий (single-peace flow) — за одну единицу времени производится и перемещается только одно изделие. Среди явных преимуществ — устранение проблемы многозадачности, выравнивание нагрузки на мощности и гибкость производства.
- канбан — система-реализация принципа «точно в срок». К плюсам относятся: прозрачность и понятность процесса разработки для команды проекта, стимулирование инициативы каждого работника, выполнение задач в срок.
- всеобщий уход за оборудованием — концепция управления и обслуживания производственного оборудования. Без этого метода невозможно представить бережливое производство.
- Система 5S — система организации рабочего места. Согласно А. Пырьеву комфортным является минимум в 9 квадратных метров рабочего пространства на одного человека. По его же исследованиям, использование офисов с открытой планировкой (персональные рабочие столы на большом пространстве) наименее эффективно с точки зрения удовлетворённости работников и производительности труда.
- быстрая переналадка (SMED) — от английского «Single Minute Exchange of Dies» — «быстрая замена штампов». Позволяет быстрее переключаться между стадиями производственного процесса, а значит уменьшать финансовые и временные затраты на создание и хранение продукции.
- кайдзен — философия, которая фокусируется на непрерывном совершенствовании процессов производства, разработки, вспомогательных бизнес-процессов и управления. В основе — 5 элементов: аккуратность, порядок, чистота, стандартизирование, дисциплина.
- Poka-yoke («защита от ошибок») — или «бака-ёкэ» («защита от дурака»). Подразумевает защиту техники, инструментов, изделий на разных этапах процесса, ПО и т.п. от очевидно неверных действий человека при взаимодействии с этими предметами.
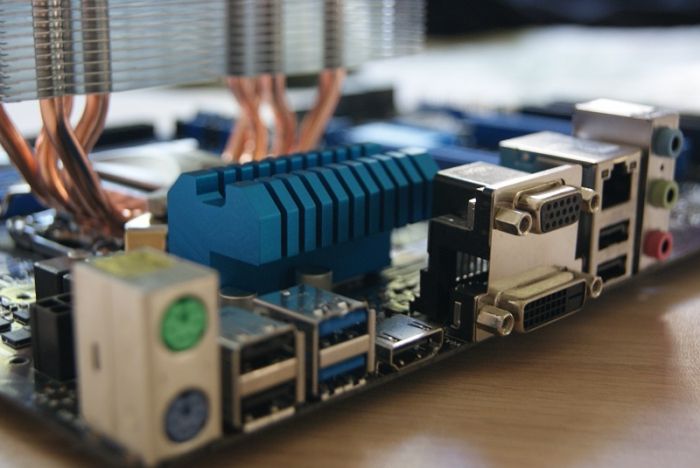
Пожалуй, вся упаковка техники в современности изготавливается по принципу пока-ёкэ. Под каждый элемент есть конкретный слот, и ошибиться в размещении невозможно.
Создание SMED
Как и концепция бережливого производства, SMED стала результатом коллаборации исследователей и производителей на протяжении XX века.
Так, в книге «Исследования движения» Фрэнка Гилберта описаны подходы к сокращению времени установки.
На фабриках Генри Форда также использовали некоторые из методов сокращения времени наладки. В публикации 1915 года «Методы Ford и магазины Ford» чётко описаны подходы к снижению времени установки и наладки производства. Но эти методы так и не стали популярными. В приоритете было наращивание объемов производства, а не оптимизация процесса.
Ford Model T 1917
А вот японской Toyota удалось воплотить бережливое производство и создать настоящее чудо. В 70-80-ых годах XX столетия западные автопроизводители не понимали, как японским машинам удаётся сочетать высокое качество при низкой цене. К сожалению, исследований на английском языке практически не было.
Но компаниям крупно повезло. Японский инженер Сигео Синго, принимавший участие в разработке методики бережливого производства, в конце 1970-ых участвовал в одном из специализированных воркшопов. После того, как он начал раскрывать подробности производственной системы Toyota без разрешения, компания быстро уволила нерадивого сотрудника.
Синго перебрался в США и начал консультировать организации по вопросам бережливого производства. Помимо того, что он заявил о своём авторстве метода быстрой переналадки, Сигео переименовал его в Single Minute Exchange of Die.
Методика реализации SMED
Для эффективного применения SMED, нужно понять, каких целей вы добиваетесь при внедрении инструмента. К общим целям относятся такие:
- снижение простоя оборудования и производственных мощностей
- сокращение запасов незавершённого производства (деталей, материалов, полуфабрикатов)
- расширение ассортимента продукции.
Важность SMED трудно переоценить.
На ЛКМЗ выяснили, что суммарно на установку и наладку оборудования уходило 56% общего рабочего времени!
Сократить объем временных и финансовых трат можно, внедрив быструю переналадку в 7 этапов:
- Разделите внутренние и внешние операции — внутренние операции выполняются только после отключения (остановки) оборудования. Замена системы фильтрации или пресс-форм возможна только при остановке конкретного механизма.
А вот для внешних отключения не требуется — те же действия по сборке и проверке системы фильтрации попадут в эту категорию. - Стандартизируйте внешние операции — в рамках этого этапа рассматриваются детали рабочего процесса с определением возможности стандартизации. Но у каждого предприятия собственное видение этой стадии.
Например, Демиховский машиностроительный завод выбрал путь стандартизации функции, а не форм и размеров штампов из-за ограничений в бюджете. Также они сделали упор на стандартизацию и регламентацию действий по переналадке — они мало затратны, но по подсчётам специалистов завода на их долю пришлось около 70% всего сокращённого времени. - Превратите внутренние операции во внешние — сам создатель Сигео Синго в книге «Быстрая переналадка» утверждал, что если бы он осознал важность превращения внутренних операций во внешние в 60-ых, то SMED было бы создано лет на 12 раньше. Японский инженер утверждал, что для выполнения этапа нужно:
+ проверить операции — возможно какие-то из них ошибочно воспринимаются как внутренние
+ найти способы превратить такие операции во внешние. - Улучшайте внутренние операции — для улучшения достаточно задать ряд вопросов, ответы на которые помогут быстро разобраться, где проблемы в производстве:
+ это лучшее время для операции? Можно сделать её в другое время?
+ это лучший человек для операции? Кто-то может выполнить работу вместо него?
+ это лучшее место для выполнения работы? Возможно ли это сделать на другом рабочем месте? - Улучшайте внешние операции — полезным будет использовать некоторые инструменты для воплощения этапа в жизнь:
+ составление контрольных листов
+ проведение функциональных проверок
+ внедрение параллельных операций. - Автоматизируйте — показательный кейс компании MPI, которые использовали по максимуму автоматизацию процессов производства. Работа оператора над изделиями из воска сводится к минимуму, и это позволило уменьшить время переналадки до 60 секунд.
- Постоянно улучшайте рабочий процесс — важно вовлекать в этот процесс всех участников: от руководства и проектного менеджера до исполнителей. Подспорьем станет план дальнейших усовершенствований с указанием приблизительных сроков внедрения.
Вердикт
SMED — один из мощных инструментов концепции «бережливого производства».
Появившись во второй половине прошлого столетия, быстрая переналадка стала ответом на растущие масштабы и неповоротливость рабочего процесса.
Благодаря внедрению Single Minute Exchange of Dies значительно уменьшаются временные задержки между стадиями производства, а значит снижается уровень ресурсных затрат.
Книги для статьи предоставлены kniga.biz.ua