В концепции бережливого производства выпуск продукции рассматривается как процесс создания ценности, в котором движутся потоки материальных и информационных ресурсов.
Процесс создания ценности
Чтобы эффективно управлять производственным процессом, устранять потери и внедрять усовершенствования, используется инструмент Value Stream Mapping — визуальное систематизирование потока ценности.
Что такое Value Stream Mapping: история и описание метода
Value Stream Mapping, VSM, дословно переводится как «составление карты потока ценности». Часто в русскоязычных источниках используются формулировки «систематизирование потока ценности» или "карта потока создания ценности«.
Value Stream Mapping — это инструмент, который визуализирует процесс превращения сырья в готовую продукцию, отпускаемую потребителям. Его объекты — материальные и информационные потоки ресурсов, а также время.
Пионер систематизирования потоков ценности — корпорация Тойота. А термин Value Stream Mapping впервые был применен в 1990 году в книге Дж. Вумека, Д. Джоунса и Д. Руса «Машина, которая изменила мир». Те же авторы развили идею VSM в книге «Бережливое производство» спустя шесть лет.
Корпорация тойота
Value Stream Mapping — это способ наглядно изобразить шаги, необходимые, чтобы потребность потребителей превратилась в продукт или услугу.
Часто Value Stream Mapping называют кайдзен потока, то есть постоянное совершенствование потоков ценности. Это лучший инструмент для выявления и планирования возможностей усовершенствования производства. Поэтому карты потоков создания ценности, КПСЦ, составляются таким образом, чтобы наглядно изобразить текущее состояние, спланировать и внедрить будущее состояние с измеримыми целями.
Использование методологии
Систематизирование потока ценности выполняется в разных масштабах — от простых административных процедур, до масштабного производства на мировой рынок. Метод помогает определить шаги, которые не добавляют ценности и подлежат устранению, а также слабые места, где процесс можно улучшить: ускорить, снизить затраты и обеспечить более безопасные условия труда.
Создание Value Stream Mapping делится на три блока:
- Производственный или процессный поток — традиционная блок-схема, в которой слева направо фиксируется путь создания ценности начиная закупкой сырья и заканчивая отгрузкой продукции. Если кроме основного процесса существуют дополнительные или вспомогательные, они наносятся под основным. Таким образом основные задачи отделяется от второстепенных.
- Информационный или коммуникационный поток — в верхней части карты потока создания ценности стрелками изображаются потоки информации, которые происходят параллельно с производством. Учитывается и формальный и неформальный обмен данными. Информационные потоки наносятся на карту в свободной форме, так, как они протекают в действительности.
- Timeline и расстояния — линии, которые рисуются в нижней части карты. Линия времени делится на верхнюю и нижнюю части. Сверху отображается lead time — время ожидания. Снизу наносится продолжительность цикла. Под линией времени может находиться еще одна линия, в самом низу, показывает расстояния, по которым продукт или персонал движутся внутри процесса.
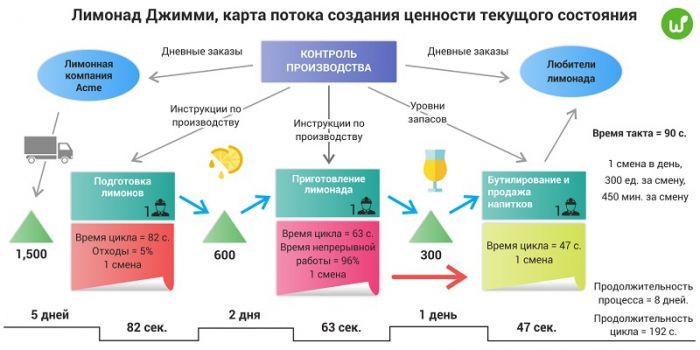
Эффект Value Stream Mapping
Составление карт потока создания ценности полезно для компании любого масштаба.
Использование Value Stream Mapping приносит результаты:
- обеспечивает видение со стороны потребителя
- использует единый язык для всех сотрудников для наблюдения за потоком ценности
- обеспечивает целостное представление о создании продукта
- помогает с первого взгляда выявить слабые места в производстве
- помогает сотрудникам глубоко понять рабочий процесс
- мощный инструмент улучшения производственных рабочих процессов
Как создать Value Stream Mapping
Применение КПСЦ состоит из трех блоков: создание карты текущего состояния, создание карты будущего состояния и составление плана внедрения мероприятий по улучшению. Недостаточно просто наглядно изобразить процесс производства — без планирования, внедрения и анализа улучшения методология Value Stream Mapping не имеет смысла.
Карта текущего состояния дают отправную точку для создания бережливого будущего состояния. Она позволяет организации найти потери, их источники и причины: если в этой точке мы несем потери, то почему процесс устроен именно так и как можно его улучшить?
Карта будущего состояния — это определение будущего идеального состояния производства. Оно может включать создание непрерывного потока, применение способов организации материального потока FIFO или supermarket там, где непрерывный поток невозможен, и выравнивание производства (production levelling). Наконец, карта будущего состояния определяет улучшения, которые нужно внедрить.
FIFO — first in, first out, первая деталь, которая попадает в процесс, первой покидает его. Детали движутся строго по порядку, и количество деталей в линии ограничено. Когда линия заполняется, предыдущий процесс останавливается.
Supermarket (супермаркет) — несколько параллельных линий FIFO, на которых движутся разные детали и продукты. Основная идея супермаркета состоит в том, что когда одна деталь или единица продукции вынимается из процесса, то сразу же замещается (по аналогии с обычным супермаркетом, когда мы берем товар с полки). При этом важно поддерживать запас всех деталей, но избегать перепроизводства.
Production levelling — метод организации производственного процесса, при котором промежуточные товары выпускаются с постоянной скоростью, чтобы дальнейшая обработка также могла выполняться с постоянной и прогнозируемой скоростью.
Самая важная часть составления карты создания потока ценности — план внедрения улучшений. Он определяет каждую активность, необходимую для достижения будущего состояния, ответственную команду или сотрудника и дедлайн. Мероприятия плана обычно относятся к событиям кайдзен или проектам «Six Sigma». Чтобы не пропустить ни одно из мероприятий по улучшению плану, их лучше прописать в task manager компании.
Пошаговое руководство по созданию VSM
Чтобы нарисовать карту потока ценности, нужно привлечь специалистов в тех областях, которые будут наносится на карту, и эксперта по составлению подобных карт. Начинать лучше с карандашного наброска на большом листе бумаги, так как правок будет много.
Шаг 1. Выбор процесса для систематизации потока ценности (подготовительный)
Допустим, предприятие выпускает много видов продукции. Чтобы упростить анализ, есть смысл объединить их в продуктовые группы. Это легко сделать с помощью таблицы:
Продукт | Шаг процесса | |||
1 | 2 | 3 | n | |
A | ✔ | ✔ | ✔ | |
B | ✔ | ✔ | ✔ | |
Z | ✔ | ✔ | ✔ |
По вертикали — выпускаемые продукты
По горизонтали — все шаги процесса
Продукты, которые проходят через одни и те же шаги, относятся к одной продуктовой группе. В нашем упрощенном примере это продукты A и Z.
Дальше выбираем продукт или группу продуктов для систематизации потока ценности по следующим критериям:
- самый дорогостоящий продукт
- продукт с самым крупным выпуском в единицах
- продукт с самым высоким показателем брака
- продукт с самым высоким показателем возвратов потребителями
- продукт, стратегически важный для будущего развития компании
- продукт, который проходит через большую часть процессов
Теперь нужно пройтись по пути создания ценности в обратном направлении — от потребителя до поставщика сырья. Посмотрите, как обрабатываются заказы клиентов, как выполняется работа в цехе, как передаются заказы вверх, как поставляются материалы и как продукты попадают с последнего шага процесса к клиенту. Когда вы получите общее представление о процессе, можно переходить к составлению карты текущего состояния.
Карта текущего состояния — шаги 2-8Шаг 2. Символы Value Stream Mapping
Существуют стандартные символы для карт потоков ценности, которые обозначают процессы, материалы, информацию. Можно отталкиваться от них или изобрести собственные, привычные и понятные.
Основные символы VSM
Шаг 3. Определение границ процесса
Нужно определить начало и конец карты. Обычно процесс создания ценности начинается с поставки сырья и и заканчивается отгрузкой продукции потребителю. Поэтому символы поставщика и потребителя и есть границы процесса, которые наносятся на карту в первую очередь. Можно копнуть глубже и учесть цепочку поставщиков и цепочку сбыта. В этом случае на карту наносятся не абстрактный поставщик и потребитель, а конкретные компании.
Шаг 4. Шаги процесса
Когда границы процесса определены, нужно разбить его на шаги — то есть операции, через которые проходит продукт. Один шаг проходит в одном месте с одной точкой входа и выхода запасов. Шаги определяются слева-направо по ходу производства и наоборот — то есть от потребителя в обратном направлении к поставщику.
Начните составлять карту с определения требований потребителей. Отметьте локацию потребителя, куда вы отгружаете продукцию, специальным символов, а в блок данных занесите требования — потребность в единицах продукции в месяц, размер отгрузки и т.д. Отметьте на карте метод отгрузки и частоту, соберите все данные о процессе. От отгрузки перейдите к запасам — сколько готовой продукции хранится на складах в ожидании отгрузки.
Дальше двигайтесь к производству. Нанесите блоки процесса для каждого участка потока материалов. Граница процессного блока проходит в месте, где процессы разъединяются и поток материалов останавливается. Соберите и нанесите на карту данные о каждом этапе и отметьте запасы, хранящиеся между блоками процесса. Закончите описание процесса обозначением блока поставщика материалов.
Шаг 5. Добавление информационных потоков на карту
Потоки информации — важная часть КПСЦ, которая отличает ее от других методов изображения производственного процесса. Информационные потоки должны описывать, как потребитель заказывает продукт, как его потребности проходят сквозь процесс вплоть до поставщиков, и как мы транслируем требования к продукту на производственно, чтобы выпустить именно тот продукт, в котором нуждается потребитель.
Шаг 6. Добавление данных о каждом шаге процесса
На этом этапе нужно привлечь команду и собрать информацию о каждом шаге процесса.
Это могут быть следующие данные:
- объем запасов
- продолжительность цикла, то есть время на обработку одной детали или единицы продукции
- продолжительность перезагрузки — время, чтобы переключиться с производства одного вида продукции на другой
- Uptime — процент времени, в течение которого машина или процесс доступны по требованию
- количество операторов
- рабочие смены
- чистое рабочее время
- процент брака
- размер упаковки или паллеты — количество единиц в партии товара на отгрузку
- EPEI — размер партии, выраженный в единицах времени: every part every ...
- количество версий продукта
Выберите подходящие измерения для процесса и запишите актуальные данные.
Шаг 7. Подсчет запасов
Избыточные запасы и перепроизводство — две из семи потерь бережливого производства, которые появляются, когда в производственном процессе есть проблемы. При подсчете запасов для карты потока ценности важно тщательно учесть все запасы, поскольку храниться они могут в самых неожиданных местах.
Шаг 8. Добавление хронологии процесса — Timeline
Timeline наносится на карту, чтобы получить информацию об общей продолжительности процесса (lead time) и времени на обработку единицы продукции (cycle time). Timeline имеет вид прямой или ломаной линии с верхним и нижним уровнями. Над линией указывается продолжительность каждого шага процесса, а под линией — продолжительность цикла обработки одной детали или единицы продукции.
Пример Timeline
Lead time — средняя продолжительность времени, за которое единица продукции перемещается через весь процесс, включая время ожидания между шагами процесса.
Cycle time — средняя продолжительность времени, за которое выполняется один или несколько шагов в пределах процесса.
Продолжительность процесса обычно составляет несколько дней — несколько недель, а длина цикла выпуска одной детали или единицы продукции — всего несколько минут. Такое соотношение показывает, как много потерь есть в системе.
Шаг 9. Карта будущего состояния
Когда вы нарисуете карту текущего состояния и определите цели бережливого производства, которых хотите достичь, — переходите к составлению карты будущего состояния. Основой для ее составления будут участки перепроизводства и потерь, которые вы выявите на карте текущего состояния.
Например:
- избыточные запасы
- длинная продолжительность цикла
- короткое время безотказной работы
- чрезмерное время установки
- низкое качество и высокий процент переделки
Отмечайте желаемые изменения на карте значками взрыва Кайдзен и корректируйте целевые значения.
Шаг 10. План Value Stream Mapping для внедрения улучшений
Финальный шаг Value Stream Mapping — составление плана действий, чтобы воплотить тот идеальный производственный процесс, который изображен на карте будущего состояния. Лучший способ составить и выполнить такой план — разбить карту будущего состояния на сегменты, и изменять один сегмент за раз.
Рабочий план должен включать метрики для измерения достижимости целей и контрольные точки.
План нужно проверять и адаптировать раз в месяц, пользуясь методикой PDCA. Когда план будет выполнен — время составить новую карту текущего состояния. Лучше всего проверять улучшения, сравнивая старую и новую карты текущего состояния, ежегодно.
Примеры карт потока создания ценности
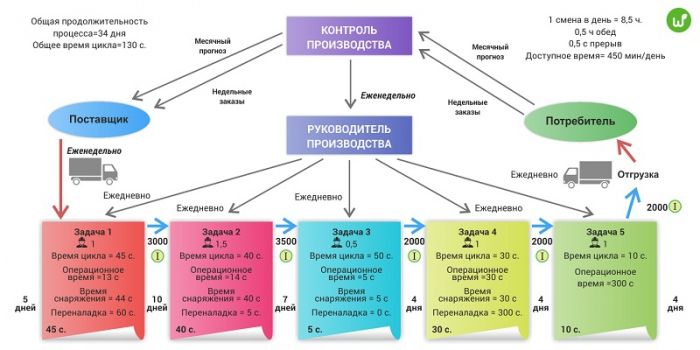
Пример value stream map
Value stream map текущего состояния
Пример карты потока создания ценности
Не обязательно рисовать карту вручную — используйте специальные программы, куда уже добавлены все символы Value Stream Mapping, вроде этих:
- Smartdraw 120$ в год, доступ нескольким пользователям
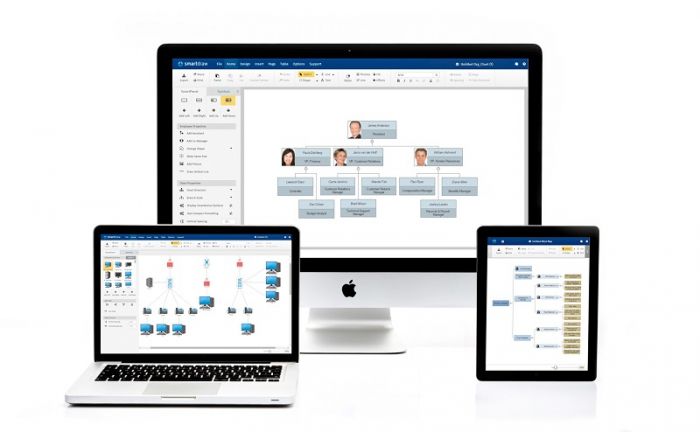
- Creately 50$ в год, доступ одному пользователю, и тарифы дороже для нескольких пользователей
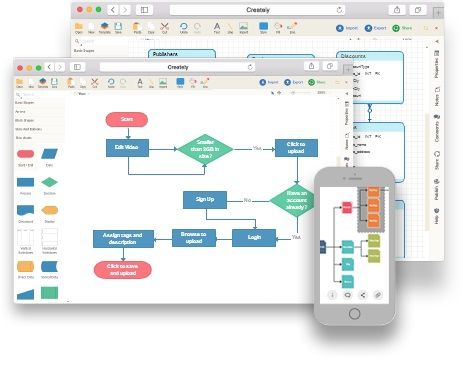
- Lucidchart 60$ в год или 6$ ежемесячно, доступ одному пользователю, другие тарифы в зависимости от количества пользователей и функций.
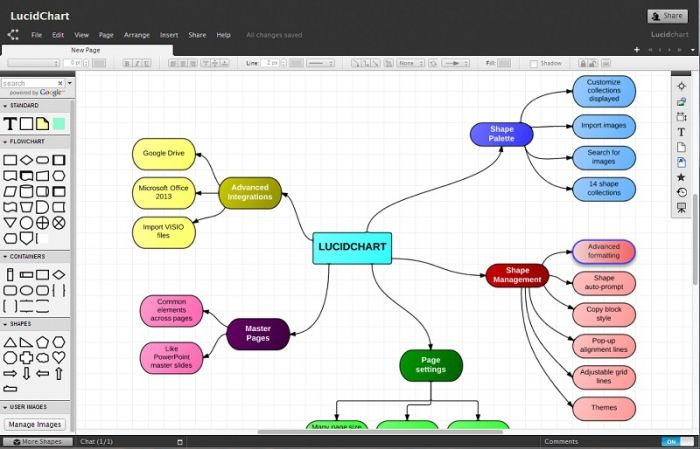
В каждой программе есть бесплатный тестовый режим — его достаточно, чтобы создать первую карту. Все программы на английском языке.
Вердикт
Визуальная информация воспринимается лучше всего, а инструмент бережливого производства Value Stream Mapping не только наглядно изображает, но и собирает воедино информацию о процессах создания ценности в компании.
Карты потока создания ценности помогают найти возможности для оптимизации процессов в соответствии с философией Кайдзен.
Систематизирование потоков ценности применяется в производстве, логистике, здравоохранении, разработке ПО, сфере обслуживания.
Deployment