Впровадження Lean methodology – оптимальне рішення для тих, хто хоче досягти успіху в бізнесі в умовах суворої конкуренції. Розпочинати впровадження слід з вивчення філософії ощадливого виробництва. Важливою складовою цього процесу є аналіз того, що таке «Lean manufacturing tools» та інструменти ощадливого виробництва.
Чого і як можна досягти за допомогою «Lean tools and techniques»?
Якщо говорити дуже коротко, то інструменти ощадливого виробництва є найкоротшим шляхом до:
- зниження витрат на якість продукції;
- прозорості управлінських процесів;
- підвищення рівня задоволеності споживачів продуктами компанії;
- зростання залучення співробітників компанії до процесу виробництва та підвищення вмотивованості;
- зменшення кількості втрат ресурсів.
Перелік інструментів з коротким описом значно спростить процес впровадження оновлень у компанії.
25 основних інструментів методології ощадливого виробництва
Інструмент | Зміст діяльності | Ефект |
5S | Належна організація робочого місця:
| Доволі швидке викриття проблем на виробництві, зумовлених неналежною організацією робочого місця, і мінімізація їх (наприклад, звільнення від завалів інструментів, які використовувалися місяць тому, а зараз лише змушують витрачати час на пошук серед них потрібного). |
Andon (Андон) | Система, що одразу ж повідомляє про проблему, яка виникла в процесі виробництва, і дає змогу зупинити процес, поки виявлений дефект не став масовим. | Вчасна ліквідація проблеми, яка дає змогу надалі не витрачати ресурси на усунення наслідків помилки в глобальних масштабах. |
Bottleneck analysis (Аналіз «вузьких місць») | Пошук «вузького» місця виробництва («пляшкового горлечка»), що не дозволяє створювати більше продукції за меншу кількість часу. Збільшення «пляшкового горлечка» покращує продуктивність та обсяг виробничих потужностей. | Відбувається вдосконалення найслабшого елемента на виробництві. |
Continuous Flow (Постійний потік) | Побудова виробничих потоків оптимальним чином. Процес, що вибудуваний правильно, не передбачає завантаження «буфера» і будь-яких тривалих зупинок між етапами виробництва. | Запобігання виникненню таких втрат, як непродумане транспортування, надмірні запаси, нераціональний розподіл час |
Gemba (Поле битви) | Створення розуміння того, що все найважливіше відбувається на виробництві, а не в кабінетах керівництва. | Менеджмент бере участь у виробничому процесі, що дає змогу зміцнити дисципліну, зменшити час реакції на можливі проблеми та отримувати інформацію з першоджерела. |
Heijunka (Планування) | Вміння планувати замовлення певним чином. Замовлення клієнтів поділяються на кілька невеликих партій, які формуються у визначеному порядку. З’являється змога виробляти різну продукцію максимально швидко і скоротити ймовірність виникнення ризиків порушення виробничого процесу на різних стадіях і зриву термінів передачі готового продукту замовнику. | Цей lean tool призводить до зниження часу виробництва та потреби мати запас матеріалів. Він дозволяє зменшити втрати шляхом того, що кожен вид продукції виготовляється частіше, а запаси (іншими словами, заморожені активи) зводяться до необхідного мінімуму. У разі вимушеної зупинки лінії, на підприємстві є вся необхідна клієнту продукція. |
Hoshin Kanri (Розробка політики) | Побудова зв’язку між «стратегією» і «тактикою»: цілями керівництва з діями представників виробництва. | Керівництво ставить цілі кожному зі співробітників і вони рухаються в їхньому напрямку. Належна комунікація між керівництвом і робітниками дає змогу зменшити втрати. У компанію має бути впроваджено таск-менеджер для використання інструменту Hoshin Kanri. |
Jidoka (Автономізація) | Обладнання піддається частковій автоматизації. Пошук проблеми відбувається в автоматичному режимі. Є можливість зупинити виробництво при виявленні помилки. | Один співробітник може контролювати роботу відразу декількох пристроїв. Це сприяє зниженню витрат на виробництво, а також мінімізує витрати на ліквідацію помилок (у порівняти з тим, якби їх було виявлено не одразу ж, а наприкінці виробничого циклу). |
Kaizen (Постійне вдосконалення) | Використання kaizen tools є об’єднанням зусиль усіх співробітників підприємства в напрямі формування особливої корпоративної культури та досягнення спільних цілей. | Ефект синергії при об’єднанні зусиль співробітників, спрямованих на зменшення витрат, перетворюється у «вічний двигун» розвитку ощадливого виробництва на підприємстві. |
JIT, Just in time (Саме вчасно) | Виробництво і система постачання базуються на «витягуванні» необхідної клієнту на цей момент часу кількості продукції. При цьому прогнозований попит до уваги практично не береться. Вимагає наявності на виробництві таких систем, як «Continuous Flow», «Kanban», «Takt time» та «Heijunka». | Такий спосіб найкраще працює за потреби у зниженні кількості виготовлених виробів, запасів сировини та розміру виробничого приміщення. Сприяє оптимізації фінансових потоків. |
Kanban (Сигнальна карта) | Регулює потоки випущеної продукції та сировини всередині та за межами виробництва. Необхідність у компонентах або готовій продукції визначається за допомогою сигнальних карт. | Знижується кількість втрат і надлишок запасів на складі. Позитивно впливає на результати проведення інвентаризації на складі. |
KPI (Ключові показники продуктивності) | Система метрик застосовується для аналізу пріоритетних сегментів діяльності компанії. Є потужним стимулом зростання для співробітників. | Ключові показники, які можуть змінювати працівники, дають змогу своєчасно визначати потенційні втрати та ризики, досягти стратегічних цілей, поставлених перед компанією. |
Muda (Втрати) | Усунення всього, що не становить цінності для замовника (споживача). | Ознайомившись з усіма можливими видами втрат, слід їх своєчасно мінімізувати, що підвищить якість роботи персоналу, обладнання та організації загалом. |
PDCA (Плануй-Роби-Перевіряй-Дій) | Ітеративний метод, що дозволяє впроваджувати різноманітні покращення та/або здійснювати зміни:
| РDCA дає змогу знаходити системний підхід у розв’язанні проблем, що виникають, впроваджувати поліпшення і здійснювати експерименти:
|
OEE (Overall Equipment Effectiveness, Повна ефективність обладнання) | Дозволяє відстежити три види втрат, що стосуються функціонування обладнання: якість, готовність, продуктивність. | Дає змогу зрозуміти, наскільки ефективно експлуатується обладнання. Це збалансований показник, що дає змогу підвищити прибутковість виробництва і поліпшити його технологічність. Якщо ОЕЕ досягає 100%, значить, компанія випускає продукт без браку, настільки швидко, наскільки це взагалі можливо з урахуванням наявних технологій, і не допускає простоїв. |
Poka-Yoke (Захист від помилки, Захист від дурня) | Створення методів, що запобігають появі помилок у процесі виробництва. Головна мета – досягти «0 % дефективності». | Витрати, пов’язані з попередженням помилок, значно нижчі, ніж ті, які компанія зазнає в разі регулярних інспекцій і під час виправлення браку, виявленого через тривалий час. |
Аналіз основних причин | Таким факторам немає місця на виробництві. Їх виявлення проводиться за принципом «п’яти чому». Тобто потрібно ставити запитання «Чому?» щонайменше 5 разів щодо кожного фактора, який негативно впливає на виробництво. | Усунення основних причин появи проблем дає змогу запобігти виникненню аналогічних ситуацій у майбутньому. |
Visual Factory (Візуалізація виробництва) | Використовуються прості індикатори. З їх допомогою здійснюється обмін інформацією. | Кожний співробітник розуміє поточну ситуацію, спираючись на дані системи інформації (колір, звук та інші сигнали). |
VSM (Value Stream Mapping, Карта потоку створення цінності) | Інструмент Lean, який дає змогу наочно відокремити процеси, котрі додають цінність, від тих, що її не створюють. | Зручне рішення для планування змін, що плануються пізніше. |
TPM (Загальне обслуговування обладнання) | Метод ощадливого виробництва, який полягає в тому, щоб залучити до обслуговування обладнання кожного співробітника компанії, а не тільки фахівців-техніків. Мета ТРМ – збільшити термін експлуатації обладнання та його ефективність. | Зменшення кількості простоїв, помилок у роботі з обладнанням, аварій. Посилення почуття відповідальності у кожного співробітника. |
Takt time (Час такту) | Показник періодичності, з якою клієнт замовляє продукцію. Також час такту може відображати часовий проміжок, у який компанія надає клієнту виготовлену продукцію. Можна розрахувати за формулою: Плановий час виробництва / Попит споживача. | Дозволяє визначити необхідну продуктивність певної виробничої ділянки з метою задоволення потреб клієнтів. |
Стандартизована робота | Керівництво щодо наближеного до ідеального виконання певної операції. Цей документ постійно аналізується та оновлюється. За наявності в компанії однакового обладнання воно має працювати за єдиним стандартизованим методом (оптимальним). Максимальна ефективність досягається при використанні інтерактивних документів, які можна швидко видозмінювати та доповнювати. | Зменшуються втрати (внаслідок застосування лише кращого досвіду). Знижуються ризики створення неякісного продукту. |
SMART (Розумні цілі) | Ця абревіатура містить у собі наступні слова: Specific, Measurable, Attainable, Relevant, and Time-Specific. Українською це звучить так: ціль конкретна, вимірна, досяжна, релевантна, визначена в часі. | У разі недостатньо продуманої комунікації або помилкового розуміння завдань неминуче виникають втрати. Усунути цю проблему дає змогу правильно поставлена ціль. |
6 причин зниження продуктивності | Серед найпоширеніших причин зниження продуктивності наступні: несправності, налаштування, нетривалі зупинки, зниження швидкості, відмова в роботі або виробництві. | Усі ці причини є закликом до дії. Скоротити час простою можна тільки при послідовному усуненні всіх проблем. |
SMED (Швидке переналаштування) | Набір tools manufacturing, заснованих на принципах ощадливого виробництва, що дають змогу набагато швидше здійснювати налаштування обладнання (до 10 хвилин). Переналагодження проводиться на основі двох дій: внутрішньої та зовнішньої. Внутрішні дії пов’язані із зупинкою обладнання, а зовнішні можуть виконуватися і при робочому пристрої. Методологія SMED передбачає трансформацію дій із внутрішніх у зовнішні. | Стає простіше виробляти невеликі партії продукції, збільшується час корисної роботи обладнання. |
Етапи впровадження інструментів Lean
Зрозуміло, що компанії, котрі усвідомили необхідність для себе Lean management, готові вносити у свою діяльність зміни, які надалі принесуть дивіденди. Але треба розуміти, що впровадити Lean manufacturing у західних компаніях багато в чому простіше.
Принаймні через те, що для них звичний менеджмент (регулярний, фіксований) і достатня прозорість внутрішніх і зовнішніх процесів. А для вітчизняних компаній ці риси, навпаки, нехарактерні. Натомість удосталь представлені різного роду формальності та бюрократія, надмірно ускладнені бізнес-процеси.
Для того, щоб впровадження інструментів Lean відбулося легко й ефективно, необхідно насамперед працювати над зміною мислення та відмовою від звичних шаблонів, які, начебто, дають результат, але насправді підводять компанії до краю прірви:
Новітня історія демонструє вкрай нерівномірний розподіл інноваційних технологій у розрізі економік світу. Це безпосередньо пов’язано з міжнародним розподілом праці, зокрема низькокваліфікованої. Що дешевша праця, то менше стимулів у бізнесу підвищувати її ефективність. У результаті такого розподілу багаті країни стають багатшими, а бідні ще біднішими…
Ольга Андрієнко-Бентц, директор з бізнес-консультування PwC Україна
Також для багатьох вітчизняних компаній головною метою, як і раніше, залишається одержання якомога більшого прибутку. У нинішніх умовах на перше місце потрібно поставити мінімізацію втрат, яка згодом гарантовано призведе до того ж самого збільшення прибутку:
Головне завдання бізнесу — це виживання, а головний принцип ділової економіки — не отримання максимального прибутку, а попередження втрат…
Пітер Друкер, один із бізнес-геніїв XX століття, відомий теоретик менеджменту
При цьому складно недооцінити важливість системності та глобальності Lean practices:
Спочатку це були точкові поліпшення, боротьба з основними втратами. Потім ми підійшли до того етапу, коли потрібна була побудова більш системного підходу, який охоплює як периметр усього підприємства, так і всі напрямки його діяльності. Ми прийшли до побудови системи безперервного вдосконалення. Це те, що зараз впроваджується на ArcelorMittal…
Юрій Калько, керівник служби з операційних поліпшень і підвищення ефективності бізнес-процесів ArcelorMittal Kryvyi Rih
До чого готуватися перед впровадженням Lean manufacturing techniques?
Щонайменше до того, що створення постійної та ефективної системи оновлення компанії та підвищення якості роботи персоналу замість розрізнених спроб тут і там «залатати» – складне завдання, що потребуватиме створення нових посад і навіть цілих структур паралельно зі скасуванням уже наявних, інвестицій та наполегливості.
Найскладніше для компанії та підрядника – це радикальні зміни в методах роботи. Варто усвідомити, що ощадливе виконання проєктів – це не миттєва трансформація, а довгий шлях навчання, спроб, аналізу та вдосконалення…
Дж. Джонфрідо, відповідальний за будівельні проєкти компанії Procter and Gamble
Кроки до ощадливого виробництва
Покроковий алгоритм впровадження може виглядати так:
- Вибір лідера, готового взяти на себе відповідальність за впровадження змін;
- Отримання знань про Lean methodology, зокрема максимально наближених до першоджерела, не викривлених. Надалі ці знання мають стати новою системою цінностей лідера, яку він і буде впроваджувати цілісно, а не як точкові напівзаходи;
- Визначення найбільш критичних сегментів діяльності компанії;
- Визначення втрат скрізь, де це можливо зробити, та їх ліквідація;
- Створення карт: поточного і перспективного стану підзвітного об’єкта;
- Практична робота з впровадження Lean, яку вкрай бажано зробити наочною для всіх зацікавлених сторін;
- Об’єднання між собою результатів, отриманих за різними напрямами.
Що почитати:
- The Gold Mine: A Novel of Lean Transformation, Freddy and Michael Balle
- Learning to See: Value Stream Mapping to Add Value and Eliminate Muda, Mike Rother
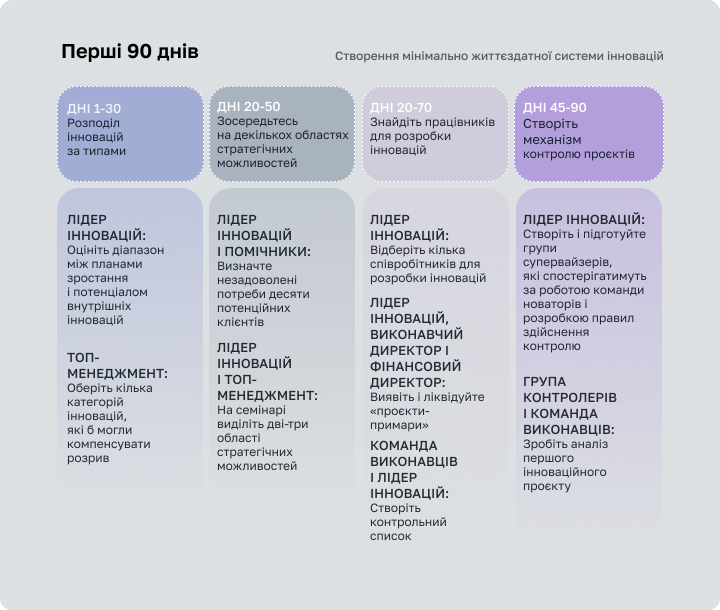
Також успіх багато в чому залежить від того, чи вийде в компанії створити наступні умови:
- показати кожному співробітнику шлях, по якому він може піти, щоб принести компанії максимум користі;
- організувати таку робочу атмосферу, в якій у кожного співробітника будуть можливості розкрити свій потенціал, використовувати Сontinous improvement tools і відкрито говорити про свої погляди на подальший розвиток бізнесу;
- сформувати ефективну взаємодію всіх підрозділів компанії, що дасть змогу додати вашому продукту максимум цінності в очах споживачів.
Що почитати:
- Інструменти ощадливого виробництва II. Кишенькове керівництво з практики застосування Lean, Майкл Вейдер (президент Lean Plus, директор групи впровадження системи «Lean Manufacturing», США)
Висновок
Ощадливе виробництво і його інструменти – життєво важливий етап у розвитку проєвропейських країн. Спершу воно застосовувалося в промисловості, однак тепер існує й ІТ інтерпретація, ба більше, навіть для сфери послуг.Застосовуйте хоча б половину цих технік, принципів і методів ведення бізнесу – і підвищення рівня якості продукту та ефективності роботи загалом буде очевидне.
Коротко, четко, понятно, с примерами.
Отлично.