5S – это инструмент Lean, который используют для постоянного улучшения рабочих условий. В процесс вовлекается как руководство, так и исполнители низших уровней.
5S – практика, которая должна быть ежедневной, а не разовой. Она требует концентрации и терпения, иначе первоначальные успехи будут напрасными.
5S зародился после Второй Мировой войны из двух японский концепций: TPM (Всеобщий уход за оборудованием) и TPS (Производственная система Toyota).
Название является сокращением от пяти японских слов: Seiri, Seiton, Seiso, Seiketsu и Shitsuke. Если адаптировать к русскому языку, то можно тоже получить 5С: сортировка, соблюдение порядка, содержание в чистоте, стандартизация и совершенствование.
Выполняя последовательно эти 5 шагов, мы добиваемся следующих целей:
- увеличиваем производительность труда
- улучшаем качество продукции за счет снижения дефектов
- уменьшаем вероятность несчастных случаев
- стандартизируем рабочие места
- создаем комфортное рабочее окружение
В ходе внедрения 5S используется циклический подход Деминга:
Планируй, делай, проверяй, воплощай в жизнь.
5 шагов
1. Seiri – Сортировка
Сперва нужно избавиться от ненужных вещей в рабочей зоне и сгруппировать нужные. На бракованные, посторонние и неиспользуемые предметы наносится красная метка, и они удаляются.
Цель первого этапа – оставить только то, что действительно необходимо.
Иначе вы будете долго искать такие вещи из-за большого количества ненужных. Либо обилие предметов будет захламлять помещение, усложняя перемещение по нему.
Действия во время сортировки:
- Осмотритесь с коллегами, чтобы найти бесполезные или ненужные вещи. Если есть сомнения о полезности, то задавайтесь вопросами: в каком количестве нужны такие предметы, как часто они используются, должны ли они храниться здесь.
- Определитесь, куда и как удалять такие вещи из рабочей зоны.
- Сфотографируйте рабочую зону до изменений.
- Нанесите красную метку на ненужные предметы.
- Выберите место, в котором будут лежать предметы с красной меткой.
- Если вы так и не решили, нужны или не нужны отдельные вещи, нанесите на них другую метку и обособьте от бесполезных.
- Подумайте, как часто используются оставшиеся в рабочей зоне предметы.
- Если ежедневно или каждый час, то они должны лежать в пределах досягаемости руки.
- Если раз в неделю или в месяц, то такие предметы можно оставить подальше в рабочей зоне.
- Выносите вещи, которые задействуются не так часто, как в пунктах выше.
- Каждый отдел обязан иметь место хранения ненужных предметов – карантин. Он обеспечивает визуальный контроль: предметы имеют четкие метки, расположены так, чтобы можно было поймать каждый в зрительный фокус.
- Поручите одному из сотрудников следить за карантином.
- Ненужные предметы могут храниться не более 3 – 4 месяцев. Уточните у работников, которые ранее использовали такие предметы или аналогичные, точно ли они не понадобятся им в дальнейшем.
- Ненужные вещи передаются на общий склад компании. Там их оценивает ответственное лицо.
- Предметы можно передать другим отделам, если там нуждаются в них. Также их можно продать. Иначе – просто выбросить.
- Сделайте фотографии рабочей зоны после изменений.
2. Seiton – Соблюдение порядка
На данном этапе нужно найти место для каждого предмета в рабочей зоне. Все должно находиться как можно удобнее и ближе в случае необходимости. Инструмент можно легко увидеть, взять, использовать и вернуть на место. В результате получается эргономичное рабочее место: минимум движений со стороны исполнителя, безопасность труда, непринужденная обстановка.
Действия во время соблюдения порядка:
- Убедитесь, что все ненужные предметы удалены из рабочей зоны.
- Держа в голове рабочий поток, подумайте, как расположить инструменты.
- Сфотографируйте рабочую зону до изменений.
- Узнайте мнение сотрудников, куда бы они расположили рабочие предметы. Они должны подумать, что им требуется для выполнения задач и в каком количестве.
- Как упоминалось в алгоритме первого шага, сортировки, часто используемые инструменты должны находиться под рукой. Используемые раз в месяц – находятся в рабочей зоне, редко используемые нужно вынести.
- Составьте план и расположите предметы в соответствии с ним. Они должны быть доступны в течение 30 – 60 секунд при минимальных действиях со стороны сотрудников.
- Убедитесь, что всем работникам сообщили о перестановках.
- Составьте подробный и четкий список предметов с их новым местонахождением. Поместите его на видное место.
- Сделайте метки на каждом шкафе или полке, что в них хранится.
- Отметьте разными линиями проходы, места хранения оборудования, источники опасности. Также обозначьте направления в рабочей зоне, размеры для инструментов в шкафе.
- Нанесите метки на все необходимые предметы.
- Сделайте фотографии после изменений.
3. Seizo – Содержание в чистоте
Рабочая зона должна ежедневно поддерживаться в чистоте. Цель не в том, чтобы помещение радовало красотой, хотя и это оказывает позитивное влияние на настроения сотрудников. 3‑й этап помогает моментально выявить дефекты и проблемы в рабочем процессе.
К примеру, утечку масла тяжело разглядеть на и так грязной рабочей поверхности. Когда же она чистая, то любое пятно сразу бросается в глаза, и проблема решается на начальном этапе.Действия во время содержания в чистоте:
- Сфотографируйте рабочую зону перед изменениями.
- Найдите способы избежать загрязнений, используя технику 5 Почему для определения причины.
- Определите и сделайте метку на предметах, которые вызывают загрязнения.
- Записывайте информацию о зонах, которые нужно привести в порядок. Для этого можно использовать таблицу:
Вопросы
Где находится проблемная зона?
В чем именно заключается проблема?
Какой сотрудник должен решить проблему?
Как решить проблему?
Когда можно приступить к решению проблемы?
Ответы
- Разработайте план и распределите обязанности.
- Сделайте уборку ежедневным процессом, результаты которого проверяются.
- Проводите уборку перед началом работы и ее завершением.
- Для каждой уборки нужно уделять от 10 до 15 минут.
- Сделайте фотографии после изменений.
5С в офисе — до и после:
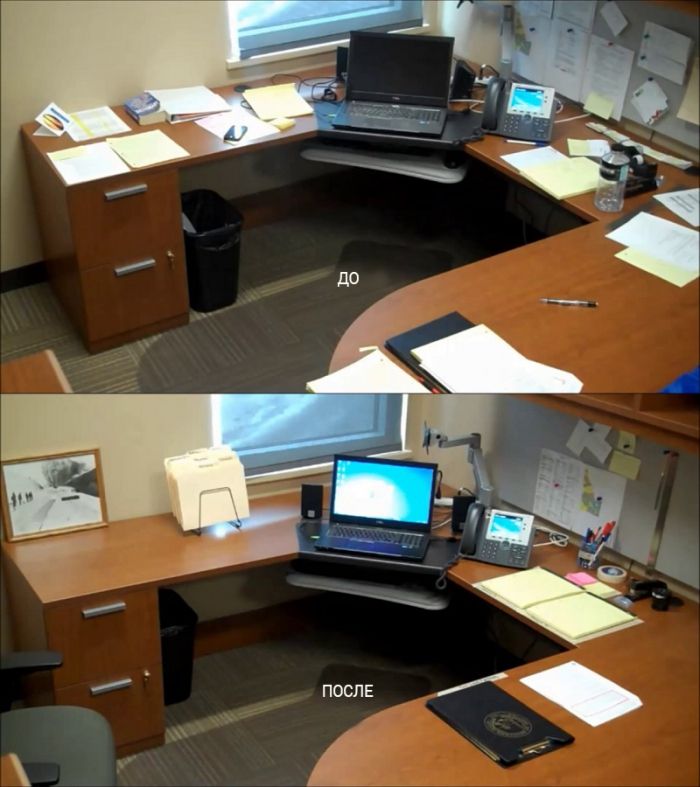
Рабочее место до и после внедрения 5С
4. Seiketsu – Стандартизация
На 4‑м этапе составляются инструкции, как поддерживать рабочую зону в чистоте, а предметы – в готовности к эффективному использованию. Если ранее сотрудникам поступали приказы и поручения, то стандартизация дает им шаблоны действий в стандартных ситуациях.
Действия во время стандартизации:
- Сфотографируйте рабочую зону перед изменениями.
- Убедитесь, что правильно внедрили 3 предыдущих этапа.
- Отобразите обязанности сотрудников в 5S и список задач на доске.
- Создайте процедуры и формы для регулярной оценки предыдущих 3 этапов.
- Создайте инструкции для задач, которые выполнялись ранее: что и как помечать красной меткой, как и куда относить ненужные предметы, как разграничивать зоны и подписывать инструменты, когда и каким образом проводить уборку, и т.д.
- Поощряйте сотрудников при удачном опыте внедрения 5S, а не критикуйте или наказывайте за ошибки.
- Сделайте фотографии после изменений.
5. Shitsuke – Совершенствование
На последнем этапе проходят обучение и тренировки. Цель совершенствования – сделать 5S настоящей культурой в организации и не вернуться к прежнему состоянию.
Действия во время совершенствования:
- Убедитесь, что сотрудники относятся к рабочей зоне с тем же вниманием, как и к своему дому.
- Раз в неделю проверяйте, как выполняются первые 3 этапа. Результаты проверок отображайте на доске. Оценивать можно по 10-балльной шкале.
- Следите, чтобы сотрудники воспринимали 5S как обязательную часть рабочего процесса, а не ждали команды или поручения.
- Руководство должно активно участвовать в инициировании и воплощении программы — например, через внедрение task manager для задач. Успешное внедрение стоит отпраздновать с коллективом.
- Применяйте технику кайзен, чтобы совершенствовать 5S.
Практическое применение 5S
Samsonite South Asia Pvt. Ltd – это расположенное в Индии представительство американской компании Samsonite, которая является одним из крупнейших производителей чемоданов в мире. Здесь производится до 40% всей продукции Samsonite.
Перед внедрением 5S индийское отделение компании испытывало такие проблемы:
- Неэффективное использование склада для хранения сырья и готовой продукции
- Трата времени на поиск материалов и инструментов из-за того, что не определено помещение для постоянного использования в качестве склада
- Снижение вследствие этого производительности
- Наличие ненужных предметов в рабочей зоне
- Для инвентаризации таких предметов требуется дополнительные затраты времени и средств
- Для хранения ненужных предметов нет специально отведенного места
- Неравномерное участие руководства и работников в организации рабочей зоны из-за отсутствия стандартов.
Методология внедрения 5S для Samsonite South Asia Pvt. Ltd:
- Обучение персонала с помощью презентаций и уроков. Ряд сотрудников индийского отделения посетили главный офис компании, где уже успешно внедрили 5S.
- Упрощение организационной структуры, схематическое объединение отделов в несколько зон.
- Проведение в выделенных зонах этапа Seizu – Сортировки – под управлением назначенных сотрудников.
- Проверка результатов сортировки и составление замечаний.
- Награждение трех лучших зон и проведение презентации для всех работников о результатах первого этапа.
- Применение следующих 4 этапов по такому же принципу.
Seiri – Сортировка на Samsonite South Asia Pvt. Ltd
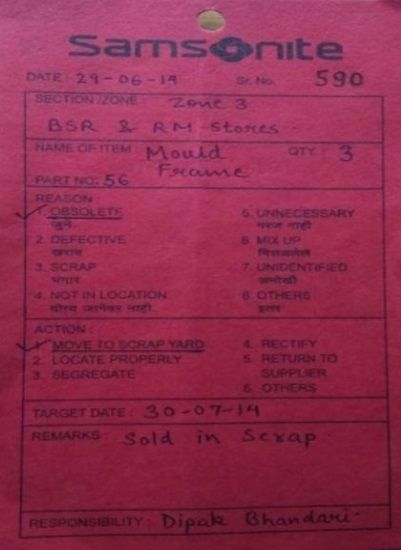
Карта для красной метки
Материалы, указанные в такой карте, отправляются в карантин или расставляются так, чтобы не занимали полезную площадь или не мешали проходу.
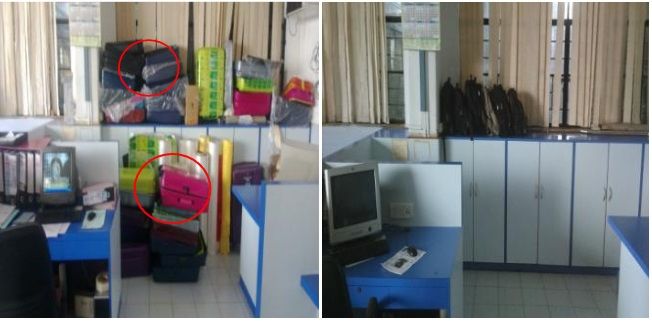
Офис отдела по литью до и после
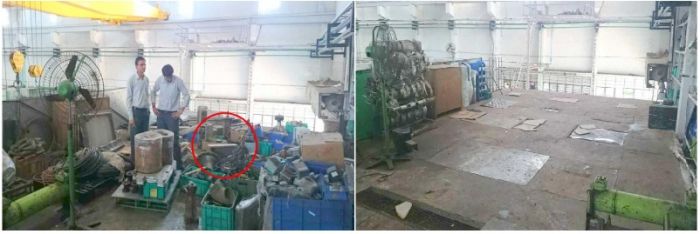
Кладовая для инструментов до и после
Seiton – Соблюдение порядка на Samsonite South Asia Pvt. Ltd
Предметы расставляются по принципу «место для всего и все на своем месте». Определяются зоны для инструментов, материалов и оборудования.
Зоны для размещения корзины для мусора, листов и образцов для станка
и щит для хранения инструментов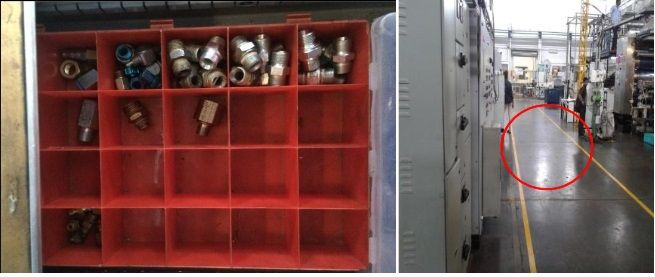
Шкаф для крепежных деталей и обозначение прохода
и щит для хранения инструментов
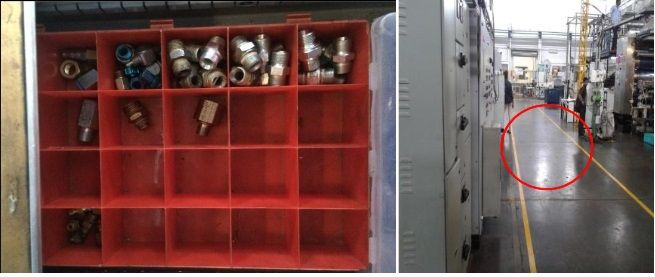
Seizo – Содержание в чистоте на Samsonite South Asia Pvt. Ltd
Проходит уборка рабочих зон, складов, офисов, проходов. Обеспечивается их дальнейшая опрятность.
Проход в цехе до и после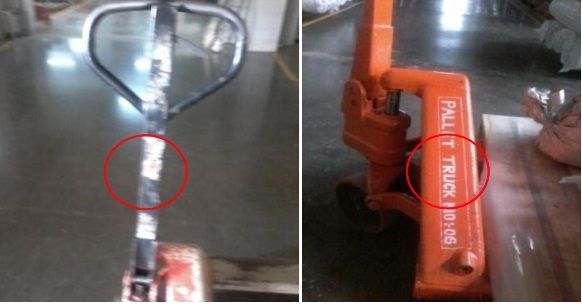
Перевозчик палет до и после
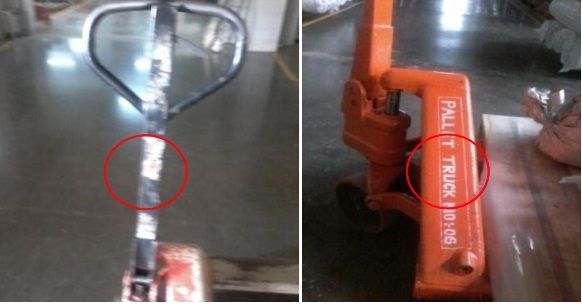
Seiketsu – Стандартизация на Samsonite South Asia Pvt. Ltd
- Были стандартизированы процедуры, которые выполнялись на предыдущих этапах. Работникам раздали инструкции на английском и родном для них языке.
- Был составлен журнал, в который вносились предметы с красной меткой.
- Сами работники, если замечали ненужный предметы, выделяли их красной меткой. Поначалу учет меток велся каждые 8 дней, затем каждые 15 дней, и в итоге один раз в месяц.
- Стали проводиться собрания сотрудников, на которых они обсуждали внедрение 5S.
Shitsuke – Совершенствование на Samsonite South Asia Pvt. Ltd
На предприятии используются внутренние проверки, часть из которых происходит без предупреждений.
Итоги внедрения 5S
- Производительность улучшилась благодаря системному подходу и грамотному расположению предметов
- Меньше времени тратится на поиск инструментов и сырья
- Огромные затраты, необходимые на инвентаризацию ненужных вещей, значительно уменьшились
- Появилось больше места для складирования мусора, сырья и готовой продукции. Проходы для работников стали намного удобнее
- У руководства и сотрудников возникла мотивация из-за равного участия во внедрении 5S
Вердикт
При полном внедрении, практика 5S поднимает настроения в коллективе и производит позитивное впечатление на заказчиков. Когда сотрудники получают удовольствие от того, где они работают, то в ходе постоянного улучшения уменьшается процент брака, ускоряется рабочий процесс и укрепляется качество продукции.
5S – это не просто система для организации рабочего места. Это культура для повышения производительности, улучшения безопасности и снижения затрат.
Чтобы 5S привел к успешным результатам, ее принципы должен понять и постоянно практиковать каждый сотрудник.